In 1982, when British Airways 9 flew through a volcanic ash cloud and flamed out all four engines, the dangers of volcanic ash were undocumented.
— James Albright
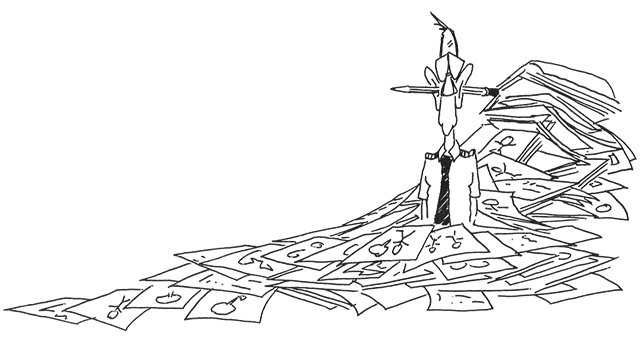
Updated:
2020-12-21
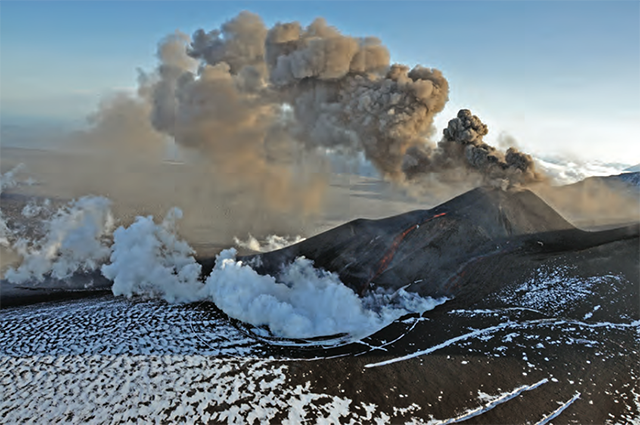
Alaska volcano, from Alaska Volcano Plan
Seven years later, when KLM 867 repeated the incident, it was clear more work was needed to detect and avoid volcanic ash. The ash is dry so does not show up on radar. It is also fine, so when it comes in contact with the airplane the static electricity makes radio communications difficult. It is abrasive, so it makes damages windshields to the point visibility is impaired. Once the particles go through the hot section of the engine they become molten and finally they recool and collect on engine turbine blades, solidifying to the point where air flow is fouled and the engines shut down. Fortunately, in every recorded case once the aircraft descends and the engines cool, the solidified ash tends to break away and the engines can be relit.
I like the Alaska Airlines Procedures for Operating in Volcanic Ash Conditions:
- When in doubt, don't fly.
- Use facts and data.
- Identify the location of both the ash and clear areas.
- Stay focused.
Gulfstream adds this cheerful note: "Has significant financial implications, may not be known until major inspection, usually considered an Act of God and is not covered by insurance."
The best plan is to avoid it in the first place and the aviation world is getting better at that. You need to stay plugged into the news and either subscribe to all the weather services that track volcanic activity or ensure your international flight planning service does. It also helps to be knowledgeable about the issue. A related post: Reading Minds.
4 — Threat Areas characteristics
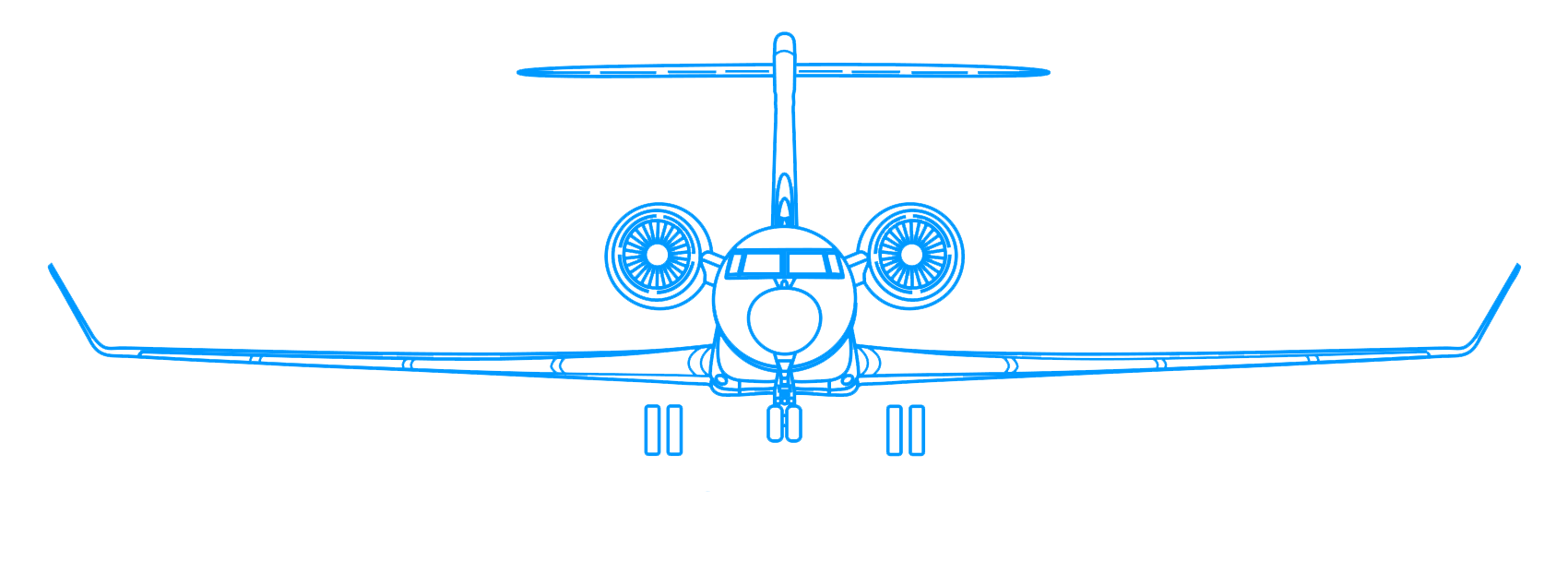
1
An overview of the threat
It seems the majority of cases involve the Boeing 747. Why is that? Before we got smart about detecting volcano eruptions and getting the word out to the aviation community, the Boeing 747 was the world's primary long distance traveller in areas where volcanic ash was likely. Any aircraft is at risk.
- Severe volcanic eruptions which send ash and sulphur dioxide (SO2) gas into the upper atmosphere occur somewhere around the world several times each year. Flying into a volcanic ash cloud can be exceedingly dangerous. A B747−200 lost all four engines after such an encounter and a B747−400 had the same nearly catastrophic experience. Piston− powered aircraft are less likely to lose power but severe damage is almost certain to ensue after an encounter with a volcanic ash cloud which is only a few hours old.
- Most important is to avoid any encounter with volcanic ash. The ash plume may not be visible, especially in instrument conditions or at night; and even if visible, it is difficult to distinguish visually between an ash cloud and an ordinary weather cloud. Volcanic ash clouds are not displayed on airborne or ATC radar. The pilot must rely on reports from air traffic controllers and other pilots to determine the location of the ash cloud and use that information to remain well clear of the area. Additionally, the presence of a sulphur-like odor throughout the cabin may indicate the presence of SO2 emitted by volcanic activity, but may or may not indicate the presence of volcanic ash. Every attempt should be made to remain on the upwind side of the volcano.
Source: Aeronautical Information Manual, ¶7-6-9
2
History of mishaps
The USGS report acknowledges that this list comprises a minimum number, since these reports are not made consistently.
There have been nine encounters with Volcanic Ash of transport category aircraft between 1953 and 2009, according to the USGS:
- 1980 May 25 — L-100 (C-130), 2 of 4 engines shut down, Mount St. Helens, United States
- 1982 Jun 24 — B-747 (British Airways 9), 4 of 4 engines failed, Galunggung, Indonesia
- 1982 Jul 13 — B-747, 3 of 4 engines failed, Galunggung, Indonesia
- 1989 Dec 15 — B-747 (KLM 867), 4 of 4 engines failed, Redoubt, United States
- 1991 Jun 17 — B-747, 2 of 4 engines failed, Pinatubo, Philippines
- 1991 Jun 17 — DC-10, 1 of 3 engines failed, Pinatubo, Philippines
- 1991 Jun 27 — DC-10, 2 of 3 engines failed, Unzen, Japan
- 2001 Jul 29 — B-767, 1 of 2 engines failed, Soufriere Hilles, Lesser Antilles
- 2006 Jul 17 — Gulfstream II, 2 of 2 engines failed, Manam, Papua New Guinea
3
Severity of the threat
- Class 0
- Sulfur odor noted in cabin.
- Anomalous atmospheric haze observed.
- Electrostatic discharge (St. Elmo’s fire) on windshield, nose, or engine cowls.
- Ash reported or suspected by flight crew but no other effects or damage noted.
- Class 1
- Light dust observed in cabin.
- Ash deposits on exterior of aircraft.
- Fluctuations in exhaust gas temperature with return to normal values.
- Class 2
- Heavy cabin dust.
- Contamination of air handling and air conditioning systems requiring use of oxygen.
- Abrasion damage to exterior surfaces, engine inlet, and compressor fan blades.
- Pitting, frosting, or breaking of windscreen or windows.
- Minor plugging of pitot-static system, insufficient to affect instrument readings.
- Deposition of ash in engine.
- Class 3
- Vibration or surging of engine(s).
- Plugging of pitot-static system to give erroneous instrument readings.
- Contamination of engine oil or hydraulic system fluids.
- Damage to electrical or computer systems.
- Engine damage.
- Class 4
- Temporary engine failure requiring in-flight restart of engine.
- Class 5
- Engine failure or other damage leading to crash.
Source: USGS, Table 1
The USGS estimates there have been 94 known ash encounters of severity 1 to 4. Three were severe enough to involve the loss of all engines and 26 created severe damage.
Engine Failures
Melting and resolidification of ash within jet turbine engines have been identified as the primary mechanisms responsible for engine failure in an ash encounter. The melting temperature of the magmatic silicate glass in ash is lower than the operating temperatures of modern turbine engines; consequently, ingested ash particles can melt in hot sections and then accumulate as re-solidified deposits in cooler parts of the engine, causing ignition flame-out and engine shutdown. In two encounters ranked as class 4, climb out from the cloud at maximum thrust was identified as a key operational condition for engine shutdown. When engine power increased, more ash-laden air was ingested by the jet turbines and combustion temperatures were raised; thus, conditions favorable for substantial melting of ash particles were met. This lesson has been incorporated into guidance to pilots about recommended actions to take during an encounter.
Source: USGS, pg. 3
[The 17 June 1991 incident] is notable in that prolonged exposure to dilute ash may have contributed to significant damage. That incident involved the same aircraft (a B747–200B) as incident 1991–14; both flights were operating between South Africa and Southeast Asia in the aftermath of the June 1991 eruption of Mount Pinatubo. In both encounters, the aircraft was operating in airspace at distances in excess of 500 km from the volcano. In [the 15 June 1991 incident], the crew noted static discharge lasting approximately an hour, but all engine parameters were normal during flight, and no problems were experienced with any of the aircraft systems. Two days later, the aircraft flew for several hours through an area coincident with remote-sensing evidence of an ash cloud before one engine lost power and a second engine was shut down by the crew. During descent, the engine that had been shut down was restarted, and the aircraft made a successful landing. These events raise the possibility of significant damage from cumulative exposure to dilute ash.
Source: USGS, pg. 5
The 2006 Gulfstream II incident is notable for involving a different mechanism for engine shutdown than melted ash. The aircraft was flying over Papua New Guinea at 11.9 km (39,000 ft) in apparently clear air with no ash or sulfurous odors noted by the cockpit crew. Between 39,000 ft and descent to 24,000, both engines failed and then were restarted; the aircraft landed safely. The operator and engine manufacturer conducted a thorough investigation, including borescope analysis of the engine and fuel analysis. The manufacturer concluded that a cylindrical filter in each fuel-flow regulator may have become blocked by volcanic ash, which at that altitude could have caused loss of fuel flow and thus engine shutdown; on descent, the increasing pressure would have substantially cleared the filter and allowed the engine to restart. The likely source of the ash was an eruption of Manam Volcano in Papua New Guinea.
Source: USGS, pg. 5
4
Threat areas
There are volcanoes all over the world, though the primary threat is the so-called "Ring of Fire" in the Pacific. The following map can be downloaded by clicking on the map to display a much larger version. Smaller, more specific maps follow.
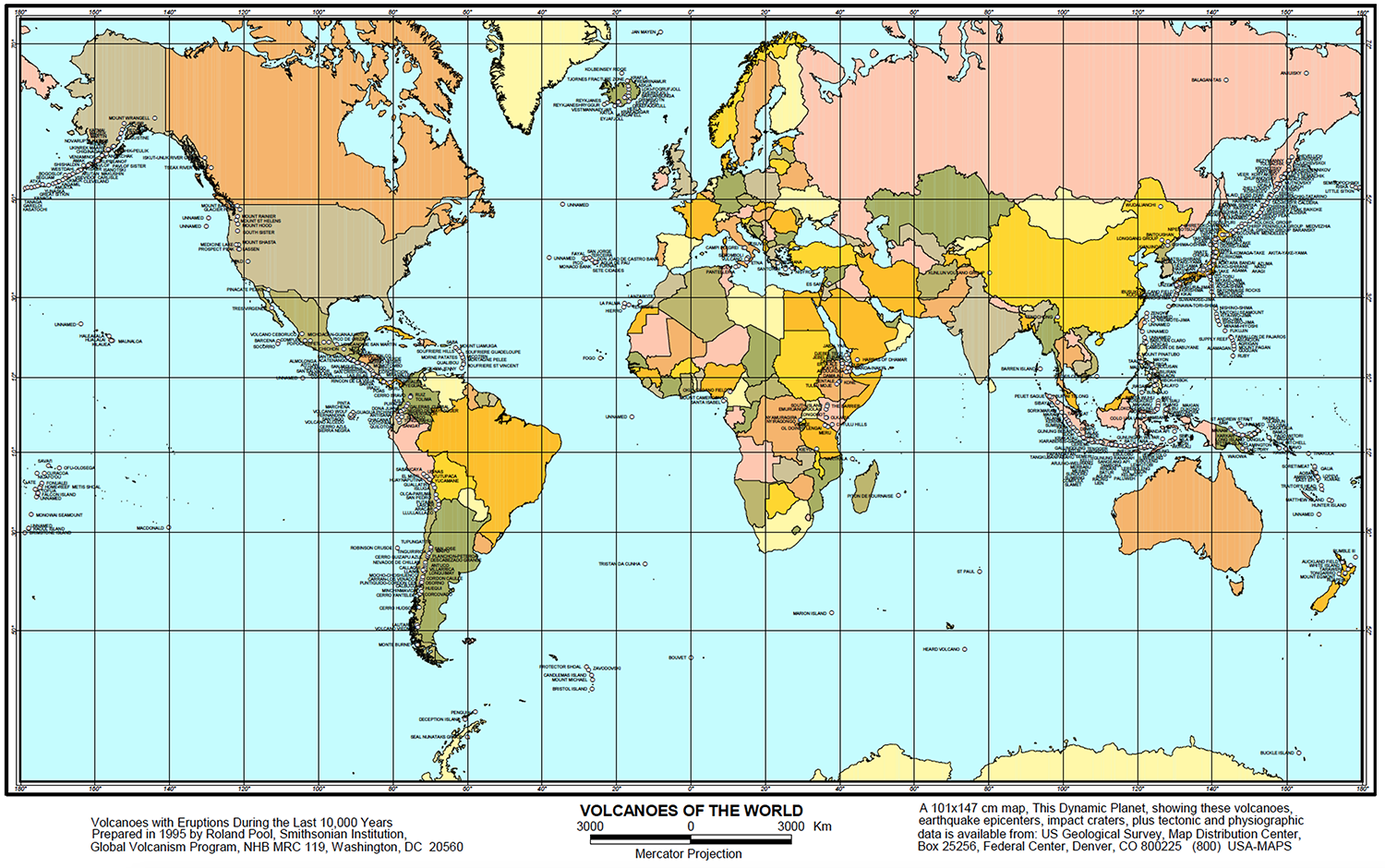
Volcanoes of the world, from (ICAO Doc 9691), pg. xi.
The highest concentration of active volcanoes lies around the rim of the Pacific Ocean, the so-called "ring of fire", which stretches northwards, more or less continuously, along the western edge of South and North America, across the Aleutian and Kurile Island chains, down through Kamchatka, Japan and the Philippines and across Indonesia, Papua New Guinea and New Zealand to the islands of the South Pacific. Other active regions are to be found in Iceland, along the great rift valley in Central and East Africa, and in countries around the Mediterranean.
Source: ICAO Doc 9691, pg. I-i_1
The Pacific "Ring of Fire"
Alaska
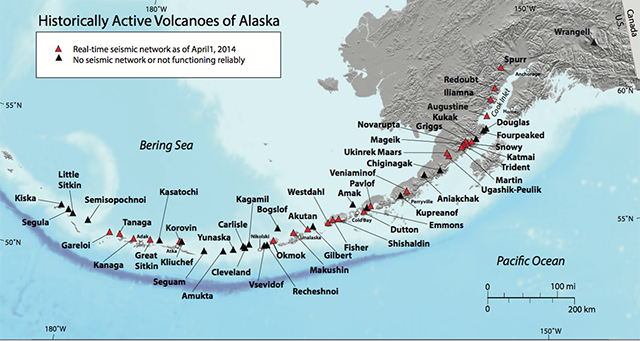
Historically active volcanoes of Alaska, from Alaska Volcano Plan, pg. 43.
Kamchatka
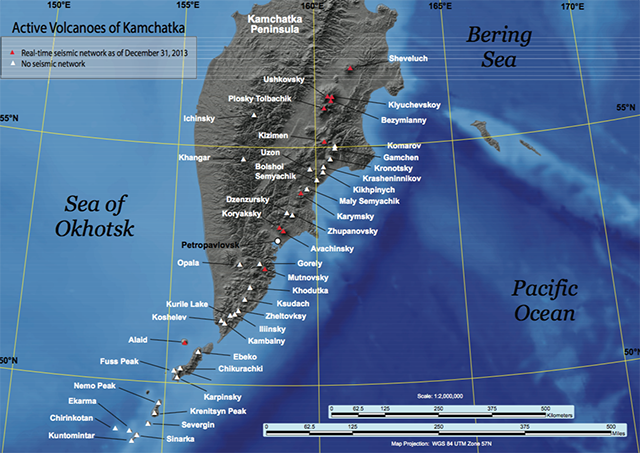
Historically active volcanoes of Kamchatka, from Alaska Volcano Plan, pg. 45.
The Kuriles
5
Volcanic ash characteristics
The Clouds
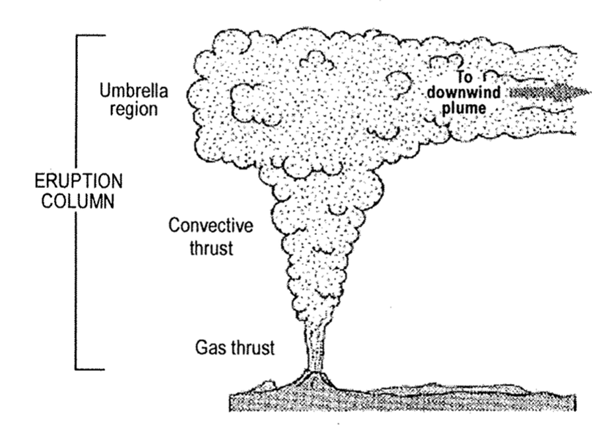
Three parts or regions from an eruption column, from ICAO Doc 9691, Figure 2-4.
- The eruption column which results is usually divided into three dynamic regimes: "gas thrust", "convective thrust", and "umbrella region" (or "mushroom") as shown in [the figure].
- The gas thrust region is produced by the sudden decompression of superheated volatile constituents dissolved in the ascending magma. This produces a jet of fluids and pulverized rock material of extremely high kinetic energy at the mouth of the volcano vent, the speed of which in extreme cases could exceed 500 kt. Such exit vent speeds may reach supersonic speed depending on the ambient conditions at the time.
- If insufficient air is entrained in the gas thrust region, the column remains denser than the surrounding atmosphere and, as the initial kinetic energy dissipates, the column collapses due to gravitation without forming a convective thrust region. The convective thrust region largely controls the ultimate height of the column and hence is critical to the eruption's potential concern to aviation. It is clear from the foregoing that the hotter the original jet of fluidized material at its release form the vent, the higher the thermal energy which can be carried through to the convective thrust region and the higher the column top.
- The third dynamic region of the volcanic ash column is the "umbrella region," to top of the mushroom-like ash cloud as its ascent begins to slow in response to gravity and the temperature inversions at the tropopause, with the top spreading radially to begin and then predominantly in one or more particular directions in response to the upper winds at different levels of the atmosphere. This region of most concern to aviation because vast volumes of airspace at normal jet aircraft cruising level of 10 to 14 km (30,000 to 45,000 ft) become contaminated with high concentrations of volcanic ash.
Source: ICAO Doc 9691, ¶2.2.1
The Ash
Volcanic ash is mostly glass shards and pulverized rock, very abrasive and, being largely composed of siliceous materials, with a melting temperature below the operating temperature of jet engines at cruise thrust. The ash is accompanied by gaseous solutions of sulphur dioxide (sulphuric acid) and chlorine (hydrochloric acid). Given these stark facts, it is easy to imagine the serious hazard that volcanic ash poses to an aircraft which encounters it in the atmosphere. Volcanic ash damages the jet turbine engines, abrades cockpit windows, airframe and flight surfaces, clogs the pitot-static system, penetrates into air conditioning and equipment cooling systems and contaminates electrical and avionics units, fuel and hydraulic systems and cargo-hold smoke-detection systems. Moreover, the first two or three days following an explosive eruption are especially critical because high concentrations of ash comprising particles up to ~10 μm diameter could be encountered at cruise levels some considerable distance from the volcano. Beyond three days, it is assumed that if the ash is still visible by eye or from satellite data, it still presents a hazard to aircraft.
Source: ICAO Doc 9691, ¶4.1
Electrical Phenomena
- The occurrence of lightning in volcanic ash columns has been reported since antiquity. Moreover, one of the prime means of recognizing that an aircraft has encountered volcanic ash is the static electricity discharge exhibited by St. Elmo's fire at point on the airframe and the glow inside the jet engines. The static electric charge on the aircraft also creates a "cocoon" effect which may cause a temporary deterioration, or even complete loss, of VHF or HF communications with ground stations.
Source: ICAO Doc 9691, ¶2.3.1
Effect on Jet Engines
- There are basically three effects which contribute to the overall engine damage. The first, and most critical, is the fact that volcanic ash has a melting point below jet engine operating temperatures with thrust settings above idle. The ash is made up predominantly of silicates with a melting temperature of 1 100°C, while at normal thrust the operating temperature of jet engines is 1 400°C. The ash melts in the hot section of the engine and fuses on the high pressure nozzle guide vanes and turbine blades. This drastically reduces the high pressure turbine inlet guide-vane throat area causing the static burner pressure and compressor discharge pressure to increase rapidly which, in turn, causes engine surge. This effect alone can cause immediate thrust loss and possible engine flame-out. Earlier generations of jet engines, which operated at lower temperatures, were probably less susceptible to this effect. The general tendency, however, is to increase engine operating temperature as each successive family of jet engines is introduced, thereby increasing power but with improved specific fuel consumption. The melting/fusing effect of volcanic ash in jet engines will, therefore, continue to be a hazard in the future.
- During the strip-down inspections, the fused volcanic ash deposits on the high pressure nozzle guide vanes were found to be very brittle at room temperature and easily broke up and fell off the nozzle guide vanes. It seems clear that this can also happen when contaminated engines are shut down in flight and then restarted. The sudden thermal and pressure shocks of the ram air during the restart process, coupled with the cooling of the fused ash deposit when the engine is reduced to idle, seem to break off much of the deposit. Moreover, subsequent operation of the engines after restart, in the clearer air outside the ash cloud, also seems to further dislodge and evacuate some of the fused ash deposits.
- The volcanic ash being abrasive also erodes compressor rotor paths and rotor blade tips (mostly high pressure section), causing loss of high pressure turbine efficiency and engine thrust. The erosion also results in a decrease in the engine stall margin. The main factors that affect the extent of the erosion of the compressor blades are the hardness of the volcanic ash, particle size and concentration, the ash particle impact velocity, and thrust setting and core protection. Although this abrasion effect takes longer than the melting fusion of volcanic ash to shut down an engine, the abrasion damage is permanent and irreversible. Reduction of engine thrust to idle slows the rate of erosion of the compressor blades but cannot eliminate it entirely while the engine is still ingesting air contaminated by volcanic ash.
- In addition to the melting/fusing of the volcanic ash and the blade erosion problems referred to above, the ash can clog flow holes in the fuel and cooling systems, although these particular effects appear to be rather variable. In ground tests of jet engines subjected to forced volcanic ash ingestion, a deposition of black carbon-like material was found on the fuel nozzles. Analysis confirmed that the contaminating material was predominantly carbon, and although the main fuel nozzle appeared to remain clear, the swirl vanes which atomize the fuel were clogged. Such a condition would render engine restart very difficult if not impossible, because there seems to be no tendency for the material to break off during restart attempts. Strip-down of the engines involved in two flame-out incidents (British Airways B747, 1982, and KLM B747, 1989), however, did not in fact show such extreme clogging of fuel nozzles and cooling systems, possibly due to insufficient exposure time to produce this effect.
Source: ICAO Doc 9691, ¶4.2
7
Ash encounter indicators
- In day visual meteorological conditions (VMC) a precursor to a volcanic ash encounter will likely be a visual indication of a volcanic ash cloud or haze. If a flight crew observes a cloud or haze suspected of containing volcanic ash they should be aware that a volcanic ash encounter is imminent and they should take action to avoid the contaminated airspace.
- Indicators that an aircraft is encountering volcanic ash are related principally to the following:
- Odour. When encountering volcanic ash, flight crews usually notice a smoky or acrid odour that can smell like electrical smoke, burnt dust or sulphur.
- Haze. Most flight crews, as well as cabin crew or passengers, see a haze develop within the aircraft cockpit and/or cabin. Dust can settle on surfaces.
- Changing engine conditions. Surging, torching from the tailpipe, and flameouts can occur. Engine temperatures can change unexpectedly, and a white glow can appear at the engine inlet.
- Airspeed. If volcanic ash fouls the pitot tube, the indicated airspeed can decrease or fluctuate erratically.
- Pressurization. Cabin pressure can change, including possible loss of cabin pressurization.
- Static discharges. A phenomenon similar to St. Elmo’s fire or glow can occur. In these instances, blue- coloured sparks can appear to flow up the outside of the windshield or a white glow can appear at the leading edges of the wings or at the front of the engine inlets.
- Any of these indicators should suffice to alert the flight crew of an ash encounter, and appropriate action should be taken to vacate the contaminated airspace as safely and expeditiously as possible.
Source: ICAO Doc 9974, ¶1.3 and 1.4
8
Pilot procedures
- The foregoing analysis of the effect of volcanic ash on aircraft forms the basis for the procedures recommended for use by pilots whose aircraft inadvertently encounter a volcanic ash cloud.
- In such circumstance, the following general procedures have been recommended:
- immediately reduce thrust to idle. This will lower the exhaust-gas temperature (EGT), which in turn will reduce the fused ash build-up on the turbine blades and hot-section components. Volcanic ash can also cause rapid erosion and damage to the internal components of the engines;
- turn autothrottles off (if engaged). The autothrottles should be turned off to prevent the system from increasing thrust above idle. Due to the reduced surge margins, limit the number of thrust adjustments and make changes with slow and smooth thrust-lever movements;
- exit volcanic ash cloud as quickly as possible. Volcanic ash may extend for several hundred miles. The shortest distance/time out of the ash may require an immediate, descending 180-degree turn, terrain permitting. Setting climb thrust and attempting to climb above the volcanic ash cloud is not recommended due to accelerated engine damage/flame-out at high thrust settings;
- turn engine and wing anti-ice on. All air conditioning packs on. Turn on the engine and wing anti-ice systems and place all air conditioning packs to “on”, in order to further improve the engine stall margin by increasing the bleed-air flow. It may be possible to stabilize one or more engines at the idle thrust setting where the EGT will remain within limits. An attempt should be made to keep at least one engine operating at idle and within limits to provide electrical power and bleed air for cabin pressurization until clear of the volcanic ash;
- start the auxiliary power unit (APU), if available. The APU can be used to power the electrical system in the event of a multiple- engine power loss. The APU may also provide a pneumatic air source for improved engine starting, depending on the aircraft model; and
- put oxygen mask on at 100 per cent, if required. If a significant amount of volcanic ash fills the cockpit or if there is a strong smell of sulphur, don an oxygen mask and select 100 per cent. Manual deployment of passenger oxygen masks is not recommended if cabin pressure is normal because the passenger oxygen supply will be diluted with volcanic ash-filled cabin air. If the cabin altitude exceeds 4 250 m (14 000 ft), the passenger oxygen masks will deploy automatically.
- In the event of engine flame-out:
- turn ignition on. Place ignition switches to “on” as appropriate for the engine model (position normally used for in-flight engine start). Cycling of fuel levers (switches) is not required. For aircraft equipped with autostart systems, the autostart selector should be in the “on” position. The autostart system was designed and certified with a “hands-off” philosophy for emergency air starts in recognition of crew workload during this type of event;
- monitor EGT. If necessary, shut down and then restart engines to keep from exceeding EGT limits;
- close the outflow valves, if not already closed;
- do not pull the fire switches;
- leave fuel boost pump switches “on” and open crossfeed valves;
- do not use fuel heat — this would be undesirable if on suction fuel feed;
- restart engine. If an engine fails to start, try again immediately. Successful engine start may not be possible until airspeed and altitude are within the air-start envelope. Monitor EGT carefully. If a hung start occurs, the EGT will increase rapidly. If the engine is just slow in accelerating, the EGT will increase slowly. Engines are very slow to accelerate to idle at high altitude, especially in volcanic ash — this may be interpreted as a failure to start or as a failure of the engine to accelerate to idle or as an engine malfunction;
- monitor airspeed and pitch attitude. If unreliable, or if a complete loss of airspeed indication occurs (volcanic ash may block the pitot system), establish the appropriate pitch attitude dictated by the operations manual for “flight with unreliable airspeed.” If airspeed indicators are unreliable, or if loss of airspeed indication occurs simultaneously with an all-engine thrust loss, shutdown or flame-out, use the attitude indicator to establish a minus-one degree pitch attitude. Inertial ground speed may be used for reference if the indicated airspeed is unreliable or lost. Ground speed may also be available from approach control during landing;
- land at the nearest suitable airport. A precautionary landing should be made at the nearest suitable airport if aircraft damage or abnormal engine operation occurs due to volcanic ash penetration; and
- because of the abrasive effects of volcanic ash on windshields and landing lights, visibility for approach and landing may be markedly reduced. Forward visibility may be limited to that which is available through the side windows. Should this condition occur, and if the autopilot system is operating satisfactorily, a diversion to an airport where an autolanding can be accomplished should be considered. After landing, if forward visibility is restricted, consider having the aircraft towed to the parking gate.
- The foregoing general procedures should be supplemented by specific procedures in the aircraft operations manual — developed by aircraft operators for each aircraft type in their fleet — dealing with the particular aircraft engine combination concerned.
- Given that the most serious threat to an aircraft from volcanic ash is the risk of multiple-engine flame-out, it is extremely important to consider the ways and means of improving the success of engine restarts in air contaminated by volcanic ash. In the United States in 1991, the Aerospace Industries Association of America (AIA) ad hoc Propulsion Committee was formed comprising AIA members and representatives from international aircraft and engine manufacturers and the U.S. Geological Survey (USGS). The mandate of the Committee was to evaluate the threat of multiple-engine flameout due to volcanic ash and to make appropriate recommendations to the aviation industry and responsible government agencies. The Committee made a number of recommendations5 but, in particular, the following bear directly on the problem of engine restart, after flame-out:
- “Aircraft manufacturers, with assistance from the engine manufacturers, should define maximum engine power levels (expressed in engine pressure ratio (EPR), fan speed (N1), and (or) exhaust-gas temperature (EGT) levels) that will minimize buildup of melted and resolidified ash on HPT nozzle guide vanes. These values should be added to flight-manual procedures and should be used only when the recommended flight idle power will not assure adequate terrain clearance.
- Aircraft manufacturers, with assistance from engine manufacturers, should consider addition of a time- delay circuit to allow an air-started engine to reach stabilized idle speed before the electrical or generator load is applied. This would facilitate engine restarts under less-than-ideal conditions.
- FAA and other equivalent government agencies should require that air crews practice engine air-restart procedures in a simulator on recurring basis. Normal and deteriorated engine start characteristics should be simulated.”
- The prime importance of the last recommendation cannot be overestimated. Engine shut-downs or flame-outs in flight are rare events which many pilots will never be called upon to deal with in their whole careers. This is further complicated by the different procedures used for air-start as compared to normal ground-start. The only solution is for pilots to be provided with a set of air-start procedures which also cover procedures in volcanic ash contaminated air and for simulator air-starts to be part of basic and recurrent pilot training.
9
Resources to avoid ash encounters
- Volcanic Ash Advisory Centers. There are nine volcanic ash advisory centers established by the ICAO to forecast volcanic activity and to inform aviators of potential hazards.
- UK Met Office provides volcanic activity forecasts when applicable.
- Smithsonian / USGC Weekly Volcanic Activity Report is updated at 2300 UTC every Wednesday with recently volcanic activity.
References
(Source material)
Aeronautical Information Manual
Alaska Interagency Operating Plan for Volcanic Ash Episodes, June 1, 2014, available at: https://www.avo.alaska.edu/downloads/reference.php?citid=3996
Gulfstream G450 Aircraft Operating Manual, Revision 35, April 30, 2013.
Gulfstream G450 Quick Reference Handbook, GAC-AC-G450-OPS-0003, Revision 34, 18 April 2013
ICAO Doc 9691, Manual on Volcanic Ash, Radioactive Material and Toxic Chemical Clouds, First Edition, 2001
ICAO Doc 9974, Flight Safety and Volcanic Ash, First Edition, 2012
USGS, Encounters of Aircraft with Volcanic Ash Clouds: A Compilation of Known Incidents, 1953-2009, U.S. Department of the Interior, U.S. Geological Survey, Data Series 545, Version 1.0, 2010
Please note: Gulfstream Aerospace Corporation has no affiliation or connection whatsoever with this website, and Gulfstream does not review, endorse, or approve any of the content included on the site. As a result, Gulfstream is not responsible or liable for your use of any materials or information obtained from this site.