Here's the theory: Water is normally injected either at the compressor inlet or in the diffuser just before the combustion chambers. Adding water increases the mass being accelerated out of the engine, increasing thrust, but it also serves to cool the turbines. Since temperature is normally the limiting factor in turbine engine performance at low altitudes, the cooling effect allows the engine to be run at higher RPM with more fuel injected and more thrust created without overheating. The drawback of the system is that injecting water quenches the flame in the combustion chambers somewhat, as there is no way to cool the engine parts without cooling the flame accidentally. This leads to unburned fuel out the exhaust and a characteristic trail of black smoke.
— James Albright
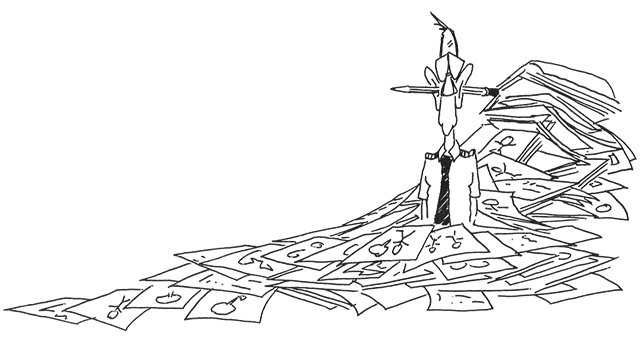
Updated:
2018-06-06
Here's the reality: Materials used to make turbine blades surpassed temperature limits early on and by the early sixties engines that could produce more thrust without resorting to water injection were common, cheaper to operate, and easier to maintain.
I flew water injected KC-135A tankers for two years and it was a pain. See Leper Crew for a short story about water injection woes.
I make the point early that this technology was quickly replaced by better materials engineering in engines, making water injection unnecessary. Well that isn't exactly true. There are still "modern" aircraft using water injection. See: Update.
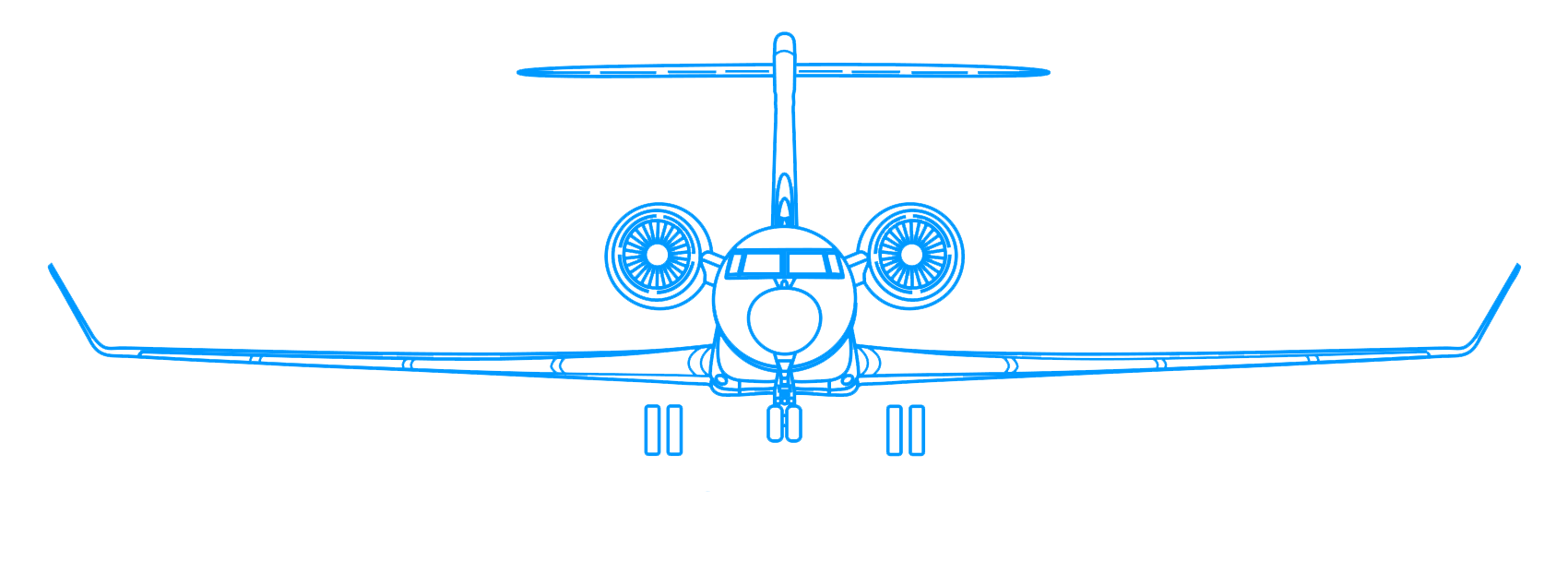
1
Misconceptions
Water injection was a great idea with older technology engines but it was inefficient and prone to failure. But the Air Force stuck with the technology long after the airlines moved on. By the time many of us got to the airplane, it was simply taught as a necessary evil, though the explanation was right in the manual. Few pilots really understood it. Case in point, this from a pilot with a lot of experience in the KC-135A . . .
Your high school science teacher lied to you-water does burn. KC-135A Pratt & Whitney model J57 engines produce thirteen thousand pounds of thrust by injecting water into inlets and combustion chambers. Six hundred and seventy gallons of demineralized water burns in about 125 seconds during a "wet thrust" takeoff. Aircrews can tell water injection is working by the quick swings of the engine pressure ratio gauge needle and a very noticeable increase in noise and airframe vibration. Wet thrust takeoffs and 1950s-era jet engines are the reasons KC-135As are called "Water Wagons." Water Wagons are too heavy for takeoff without water, too heavy for takeoff with 165,000 pounds of fuel. If our aircraft does not get water injection, my crew stays home, becoming the new Spare Crew watching everyone else go to war. No one wants to stay home.
Source: Hasara, p. 8
First point: water does not burn and that was not its purpose in this engine. More about that below. Second point, if the conditions were right, you could actually takeoff with a failed system so long as you could dump the water during flight. Final point: I included this "excerpt" to illustrate that pilots don't need to understand the science behind their aircraft to fly them.
2
Example system
A water injection system provides thrust augmentation by allowing water to be sprayed into the air inlet and diffuser section of each engine. Water injected in this manner serves to increase the density of inlet and combustion air allowing increased thrust.
Source: KC-135A Flight Manual, pg. 1-7
In the case of the KC-135A, 5,000 lbs of heated water boosted the thrust of each engine from around 9,000 to 12,000 lbs of thrust. The plumbing was complicated and prone to failure.
3
Update
A friend sent me this photo, showing what can happen to the turbine section of an engine when "someone got lazy with the water filtration process" in a water injection system. This comes from an AV-8B Harrier in 2018.
References
(Source material)
Hasara, Mark, Tanker Pilot: Lessons From the Cockpit, Simon & Schuster, New York, 2017
Technical Order 1C-135(K)A-1, KC-135A Flight Manual, USAF Series, 25 April 1957