A doctor who jeopardizes a patient's life through unskilled, improper, or negligent treatment is guilty of medical malpractice. Any person in the maintenance profession — from the lowest mechanic to the highest VP — can be guilty of maintenance malpractice through unskilled, improper, or negligent treatment of an airplane. Malpractice. Is that too strong a word? No.
— James Albright
1
Issue 1: training
We take for granted that pilots need to be educated on wide range of subjects, not just the act of flying an airplane. For example, any good instrument pilot should be well versed on the workings of the inner ear to better understand the impact of human physiology on perceptual problems when flying without outside references. For some reason we don't expect this wide area of expertise from our mechanics. We also don't insist on a regimen of recurrent training to make sure the knowledge sticks. Both of these factors can have disastrous effects.
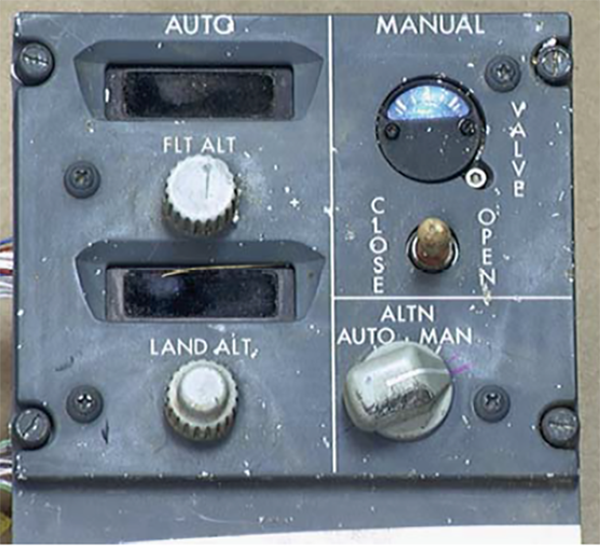
Pressurization Panel, from Helenic Republic Accident Report, pg. 51.
Take the case of Helios 522 for example. The Boeing 737 had a rapid depressurization attributed to the rigging of a service door. After the door was adjusted the Boeing manual called for a pressurization check involving a normal cabin pressure differential of 4.0 psi with the outflow valve closed and timing the cabin leak rate. Instead the mechanic simply ran up the pressure to maximum differential and assumed that if that was possible, there was no leak. After completing this non-standard check the mechanic left a switch in the wrong position. The flight crew should have caught the switch position but did not. They also made a few other mistakes that could rightfully be called the true cause of the crash, but it all started with the mechanic's failure to follow Boeing procedure. Had the mechanic been better trained to understand the reason behind the slow leak rate check versus his own invented procedure, 121 lives could have been spared. For more about this, see: Helios 522.
Recommendation: Mechanics should be trained on aspects of aviation well beyond the nuts and bolts of their profession.
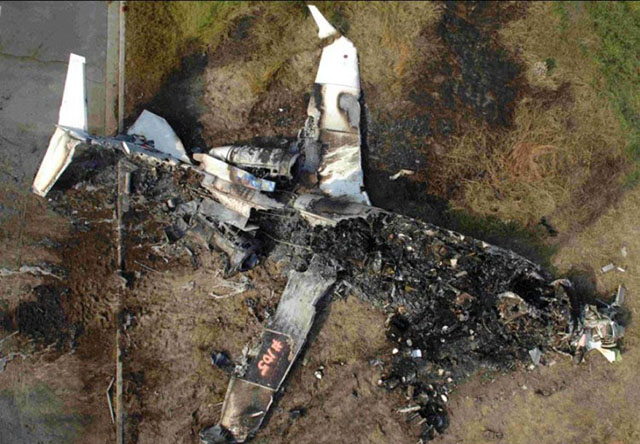
Learjet 60 N999LJ, from Aviation-Safety
There is just so much to know as a pilot we not only have to learn everything, we have to set up a schedule of recurrent training to make sure we remember the important stuff. We are given written and practical tests to make certain we have the critical items covered. Best practices say we should do that every six months. You could argue that in many ways a mechanic has to know much more, albeit a different set of knowledge. Why then doesn't a mechanic have to attend regular recurrent training?
For example, an aviation mechanic learns early about the combined impacts of osmosis and mechanical seal leakages on tire inflation; and therefore the need to regularly check tire pressures. But we often go weeks or months without checking the tire inflation on our automobiles and it can be tempting to think the process is not any more critical for an airplane. Perhaps a refresher course could have saved the occupants of a Learjet that was lost during a takeoff in 2008 when tires that had not been checked in three weeks exploded. For more about this, see: LR-60 N999LJ.
Recommendation: Mechanics should be formally retrained and tested on a variety of critical subjects on a recurring basis.
2
Issue 2: arrogance
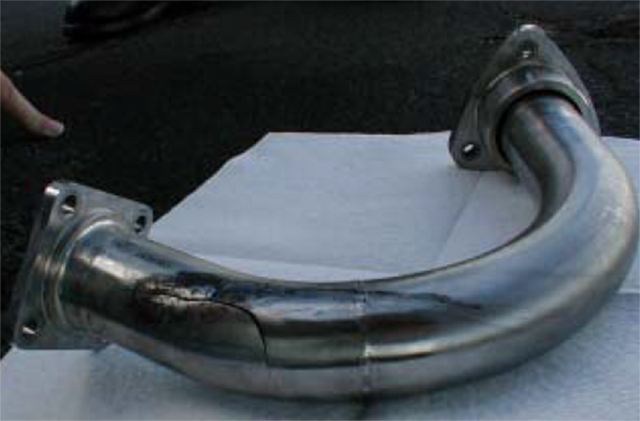
Fuel Pipe Crack, from Portugal Accident Investigation Final Report, Figure 4.
Flying an airplane is an unnatural act, given that we are seemingly defying gravity. We therefore tend to assume the stick and rudder aspects can defy our ground-based common sense and that we have to take on faith the extra steps needed along the way. But when it comes to maintaining and repairing an airplane, we often let our inner shade tree mechanic take over. In many of the case studies presented below, the mechanic thought he knew better than the manufacturer what size bolt to use, what torque needed to be applied, or other aspect of the work to be done. But the mishap can also be caused by someone sitting at a desk making decisions for the person turning the wrench.
In the case of Air Transat 236, the airline wanted the Airbus 330 returned to service with a new engine, even when a mechanic protested that the old hydraulic pump could not be safely used with the new engine assembly. The company forced the mechanics to force the pump into place, causing metal-to-metal abrasion of a fuel line. The result was a fuel leak and complete fuel exhaustion. The pilots made a number of mistakes, no doubt about it. But the event that started this chain of events happened behind a desk of an arrogant decision maker who thought he knew better than the airplane's designers. For more about this, see: Air Transat 236.
Recommendation: Maintenance manuals are not always written with the greatest of care and mechanics are often required to read between the lines or fill in the missing details. But they should do that with great caution. When deviating from written guidance anyone involved with aircraft maintenance should take the extra precaution of getting an outside opinion, the aircraft manufacturer is the perfect place to start. You should be careful who you listen to, even when talking to the manufacturer's experts. Gulfstream, for example, has a structure set up just to handle these kinds of questions. But you can get very different answers depending on who picks up the phone.
3
Issue 3: fatigue
Of all the mishap case studies presented here, perhaps none more than this one shows how one person with a wrench can cause a disaster. This mechanic couldn't be bothered to look up the right part number for the 90 bolts securing a pilot's windscreen and even when given the correct part number thought he was better off matching one of the bolts he removed with those in a parts bin. He also believed his one-step torquing procedure better than the two-step procedure mandated by the manufacturer. The windshield blew out explosively on the next flight as the airplane climbed through 17,000' and nearly took the captain with it. If it weren't for the heroic efforts of the cabin crew holding onto the captain's legs and the first officer's efforts to get the airplane on the ground as soon as possible, this accident would have done far worse than to injure two people. (The captain had several broken bones, bruises, and frostbite. One of the cabin crew had multiple injuries incurred while grabbing for the captain.)
Now why would any sane person make all these conscious decisions? I like to say that no pilot wakes up with the thought, "Today I shall crash an airplane." In a similar vein, no mechanic starts a job with the thought, "Today I shall sabotage my airplane." The mishap report notes fatigue as a factor. This particular mechanic switched from day shifts to night shifts and had only one and a half hours sleep before his first night shift in five weeks. Did that color his judgement? Perhaps. For more about this, see: British Airways 5390.
Recommendation: Mechanics should have the same pre-duty rest and duty day limitations as pilots.
4
Issue 4: short cuts
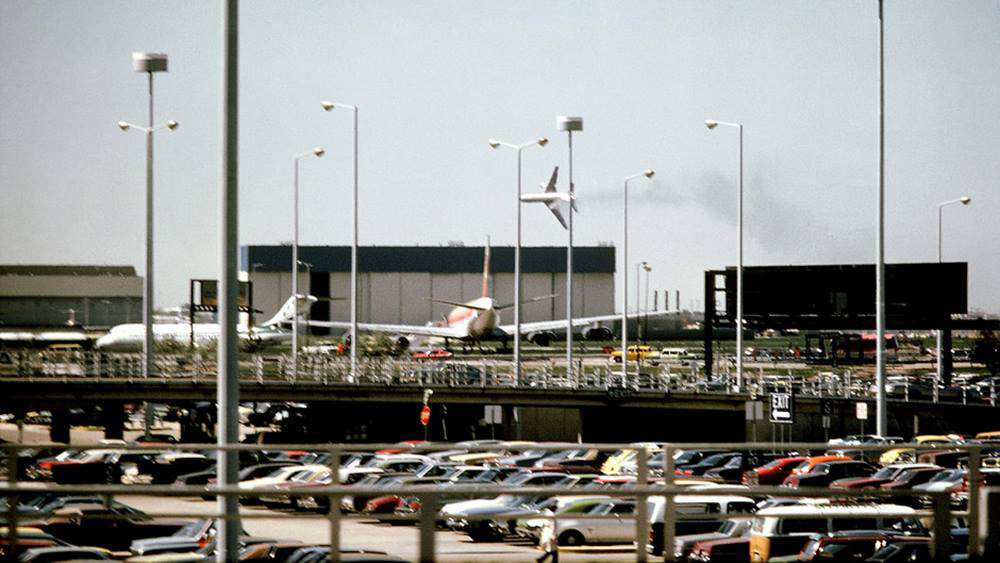
Flight 191, from Chicago Tribune
As it turns out, you can save over 200 man-hours when you replace a wing-mounted engine on a DC-10 if you use a forklift and keep the engine attached to the pylon, contrary to the manufacturer's recommended procedure to treat the engine and pylon in two separate steps. You can even tell yourself that what you are doing is safer since it reduces the number of disconnects and re-connects of the various electrical, fuel, and hydraulic lines. But sometimes these procedures have already weighed these factors and if you want to take a maintenance short cut without the risk of killing 273 people, you should stick with the proven solution. For more about this, see: American Airlines 191.
Recommendation: Any efforts to skip, reorder, or combine maintenance procedures steps should be made with great caution. You should get the manufacturer's vote and give their vote more weight than what you have seen in the field. If you have compelling evidence in favor of the procedure you should be able to convince them and your peers to also adopt the change. If you are taking the short cut on your own, it may be that you are guilty of maintenance malpractice.
5
Issue 5: quality assurance
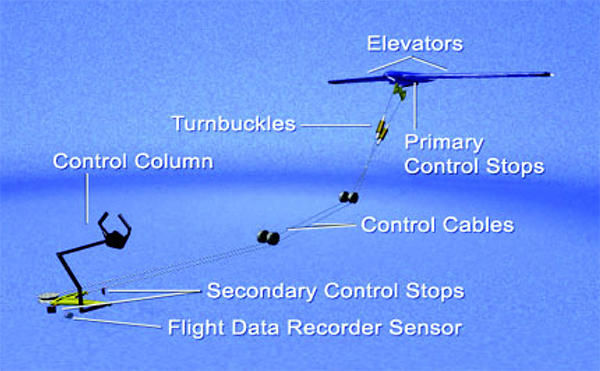
Beech 1900D pitch control system, from NTSB AAR-04/01, figure 4.
One of the safety features of flying a transport category airplane is that you almost always have a second set of eyes right next to you, making sure you are doing everything just as you have been trained and are not taking any overly risky short cuts. This additional pilot may insure against the risk of fatigue and may keep you from a false sense of confidence (preventing arrogance). In short, this additional pilot acts as a cockpit quality assurance.
What about a single mechanic playing the role of an entire maintenance shop, including quality assurance? Even in a large organization we sometimes turn a highly experienced mechanic loose with no supervision or oversight. A quality assurance inspector played the role of instructor, mechanic, and quality assurance while allowing a Beechcraft 1900D be mis-rigged to the point it became unflyable. The very next flight became the only real functional check of his work, and that flight resulted in killing all on board. For more about this, see: Air Midwest 5481.
Recommendation: Critical maintenance tasks that can result in crippling an airplane should never be completed solo. There should always be a quality assurance step carried out by a second, knowledgeable mechanic. If you don't have one you should contract for one. At the very least you ought to have a pilot study the procedure and give a final thumbs up or down to the work as performed.
6
Case studies
Most cases of maintenance malpractice touch upon more than just one of these five issues. For example . . .
Air Midwest 5481 — What caused this crash? The airline allowed a quality assurance inspector, who was too self-assured, to instruct two new mechanics on an elevator rigging procedure while also filling the role of inspector. He allowed the trainees to skip several critical steps and then passed their work in his inspection. The airplane pitched up uncontrollably after takeoff and everyone on board was killed.
Maintenance Malpractice Issues | ||||
Training | Arrogance | Fatigue | Short Cuts | Quality Assurance |
✓ | ✓ | ✓ | ✓ | ✓ |
Air Transat 236 — What caused this crash? The airline's insistence on returning an airplane to service with a new engine and the wrong hydraulic pump despite a mechanic's protest. The pump abraded a fuel line causing the airplane to leak fuel from the engine. Now why would that cause a crash? Oh yes, the pilot's misdiagnosed the leak and sent all of their available fuel to the engine doing the leaking.
Maintenance Malpractice Issues | ||||
Training | Arrogance | Fatigue | Short Cuts | Quality Assurance |
✓ | ✓ | ✓ |
Alaska Airlines 261 — What caused this crash? A poor design in the horizontal stabilizer jack screw and a maintenance crew that overlooked an earlier mechanic's findings that the jack screw needed to be replaced.
Maintenance Malpractice Issues | ||||
Training | Arrogance | Fatigue | Short Cuts | Quality Assurance |
✓ | ✓ | ✓ |
American Airlines 191 — What caused this crash? A poor design in the DC-10 engine pylon made engine removal/replacement difficult, an ill-advised modification of the procedure made by the airline damaged a pylon component, and mechanics who knew there was a problem but never reported it.
Maintenance Malpractice Issues | ||||
Training | Arrogance | Fatigue | Short Cuts | Quality Assurance |
✓ | ✓ | ✓ |
British Airways 5390 — What caused this mishap? A mechanic who couldn't be bothered to look up the correct part numbers for bolts used to secure the pilot's windscreen, who thought he knew better than the designers on what torque setting to use when securing the bolts, and ignored the advice of the person behind the parts counter about the correct bolt size. His judgement may have been impacted by a lack of sleep when changing from day cycles to the night shift and by the fact he was a supervisor who wasn't subjected to oversight.
Maintenance Malpractice Issues | ||||
Training | Arrogance | Fatigue | Short Cuts | Quality Assurance |
✓ | ✓ | ✓ | ✓ |
China Airlines 611 — What caused this crash? I believe the cause was an airline management that encouraged short cuts to manufacturer repair procedures, mechanics who were either unaware they were not using correct repair techniques or agreed to these techniques despite their knowledge, and improper oversight from the Chinese authorities. This sort of maintenance malpractice is often deadly and in this case it was.
Maintenance Malpractice Issues | ||||
Training | Arrogance | Fatigue | Short Cuts | Quality Assurance |
✓ | ✓ | ✓ | ✓ |
Colgan Air 9446 — What caused this crash? Mechanics taking a short cut when replacing an elevator trim cable which caused the electric trim switches to work backwards. The pilots could have saved the day by doing a proper preflight and following their checklists to set the trim correctly before takeoff. But they did not.
Maintenance Malpractice Issues | ||||
Training | Arrogance | Fatigue | Short Cuts | Quality Assurance |
✓ | ✓ | ✓ | ✓ |
Eurocopter AS350-B2 N37SH — What caused this crash? An improperly reused part and a missing part, that's what. But how did this happen? The mechanic and inspector had switched from night to day shifts. The mechanic had a lack of recent sleep and the inspector had been on duty for too long. But how did that happen? The FAA refused to institude pre-duty rest minimums and duty time limits for mechanics.
Maintenance Malpractice Issues | ||||
Training | Arrogance | Fatigue | Short Cuts | Quality Assurance |
✓ | ✓ | ✓ | ✓ |
Helios 522 — What caused this crash? A mechanic who thought he knew better than the manufacturer how to test a pressurization leak and left a switch in the wrong position. Of course that was just the starting link to this chain of events on the way to losing all on board this 737. The pilots failed to detect the miss-set switch and misinterpreted a warning horn.
Maintenance Malpractice Issues | ||||
Training | Arrogance | Fatigue | Short Cuts | Quality Assurance |
✓ | ✓ | ✓ | ✓ |
Japan Air Lines 123 — What caused this crash? Repairs to the aft pressure bulkhead in 1978 were made with an improper splice for an unknown reason. (Did the maintenance team misunderstand the instructions? Were the mechanics too tired to properly focus on the task at hand? Was it a simple mistake?) Inspectors failed to notice the improper splice, which should have been detectable. The improper splice held for seven years. (Until it didn't.)
Maintenance Malpractice Issues | ||||
Training | Arrogance | Fatigue | Short Cuts | Quality Assurance |
✓ | ✓ | ✓ | ✓ |
LR-60 N999LJ — What caused this crash? The organization's director of maintenance did not have a firm grasp on how often the airplane's tires needed to be checked; they hadn't been checked for three weeks. The first tire failed just after V1 but the captain's abort indecision and subsequent failure of the airplane's weight on wheel switches ended up with an abort attempt with all main gear tires failed and the thrust reverser system producing forward thrust. Lots of mistakes, yes. But it all started with failure to check tire pressures.
Maintenance Malpractice Issues | ||||
Training | Arrogance | Fatigue | Short Cuts | Quality Assurance |
✓ | ✓ | ✓ | ✓ |
7
The prescription
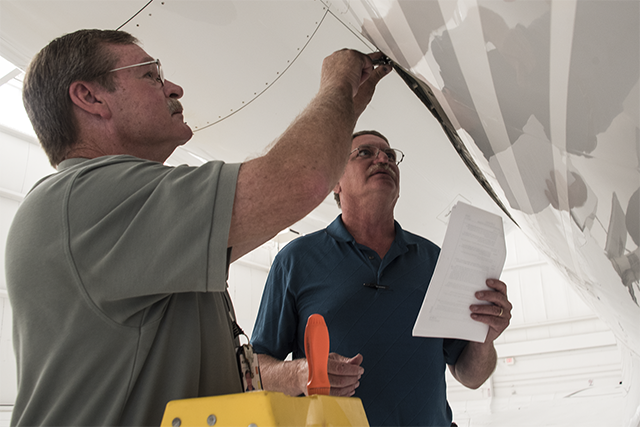
Gulfstream mechanic John Rockwell working on his G450 with mechanic Mark Paul providing quality assurance
We see a common thread with many of these case studies involving maintenance malpractice. The mechanic, the organization, or both were motivated to get the job done more efficiently. Completing a repair or inspection more quickly frees the mechanic for the next task and saves the company money. Getting the airplane back in service earlier makes everyone happier. But this motivation can lead to unsafe shortcuts and missed opportunities for proper quality assurance.
Another common theme in many maintenance related mishaps derives from a shortage of resources, usually manpower. We tend to push our mechanics harder than flight crews because we can; there are no regulatory limits on pre-duty rest or duty day duration. Tired mechanics, like everyone else, make mistakes.
In the most critical cases, the first opportunity for a quality assurance check is during the next flight. We obviously shouldn’t be performing an operational check during flight that can be done with the airplane safely chocked on the ground. From accident statistics it seems most of us are doing this right, or perhaps most of us have been lucky. In either case it would be wise to give ourselves a “heading check.” We need to self assess our maintenance programs to either pat ourselves on the back or give a needed heading correction.
- Check staffing levels. If our mechanics are routinely putting in more than 8 hours each workday we might have a problem. There are other ways to evaluate staffing levels that may not be as obvious, such as divorce rates, drug or alcohol abuse, and frequent hospitalization. These and other events can be symptoms of an overworked maintenance staff.
- Establish pre-duty rest and duty time limits. Consider establishing duty-time regulations for maintenance personnel that take into account factors such as start time, workload, shift changes, circadian rhythms, adequate rest time, and other factors shown to affect maintenance crew alertness. The FAA recently released a Draft Advisory Circular 120-MFRM, “Maintainer Fatigue Risk Management,” that provides an excellent starting point.
- Evaluate training programs. Pilots are expected to attend regular recurrent training and mechanics should not be any different. Training events should also be varied to incorporate other aviation related subjects. Consider private pilot flight lessons for your mechanic, for example. A mechanic who understands the mechanics of flight is better prepared to keep your airplane flying.
- Institute “suitability of task” rules. There are certain maintenance functions that should never be attempted by a single mechanic, such as replacing a landing gear strut on a large aircraft. (It is just too dangerous.) There are some tasks that are beyond a field mechanic’s expertise, such as replacing components inside an Engine Electronic Control. (It is just too intricate.) And there are other tasks that while not risky or complicated, require tooling and lots of help to accomplish safely.
- Ban undocumented short cuts. It is true that not all maintenance manuals are clearly written with enough detail to specify each step of a job. But inventing a new process on the fly is a recipe for missing something critical. Short cuts should be considered away from the airplane and documented. The manufacturer should be consulted. A good short cut may find a home in the next maintenance manual revision.
- Implement “Work Cards” for maintenance procedures. Pilots use checklists because the cost of skipping something important is too high. A checklist-like work card can serve to compensate for some shortcomings in training, can keep a fatigued mechanic on task, and can minimize the temptation to take short cuts. A quality assurance inspector should have a separate work card for the same reasons. As the NTSB recommended in their accident report on Eurocopter N37SH: "Using work cards that clearly delineate the steps to be performed and critical areas to be inspected to support both the maintenance and inspection tasks is one way to mitigate inadvertent errors of omission in the performance and verification of maintenance tasks, especially tasks involving critical flight controls."
- Consider real quality assurance. Failure-critical tasks should not be signed off as airworthy without a second set of eyes. Even something as routine as a tire change can have disastrous consequences if completed incorrectly. Mechanics should develop networks where another A&P can quickly inspect a repair and informally agree everything is in order. At the very least, the work should be explained and shown to the next flight’s captain.
References
(Source material)
Draft Advisory Circular 120-MFRM Maintainer Fatigue Risk Management, U.S. Department of Transportation, undated
Hellenic Republic, Air Accident Investigation & Aviation Safety Board Aircraft Accident Report, Helios Airways Flight HCY522, Boeing 737-31S, at Grammatiko, Hellas, on 14 August 2005
NTSB Aircraft Accident Report, AAR-04/01, Loss of Pitch Control During Takeoff, Air Midwest Flight 5481, Raytheon (Beechcraft) 1900D, N233YV, Charlotte, North Carolina, January 8, 2003
Portugal Accident Investigation Final Report, All Engines-out Landing Due to Fuel Exhaustion, Air Transat, Airbus A330-243 marks C-GITS, Lajes, Azores, Portugal, 24 August 2001