Cabon-carbon brakes are not like the steel brakes most of us grew up with and the techniques to extract maximum performance and maximum brake life are different.
— James Albright
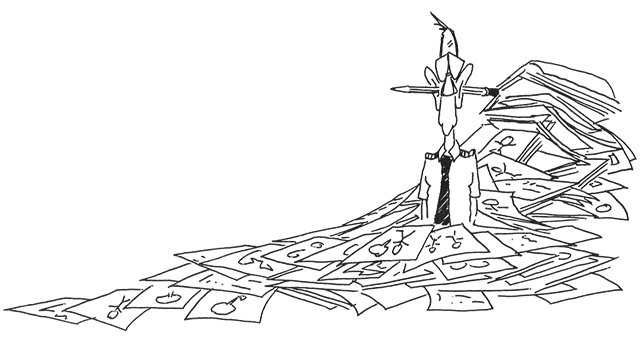
Updated:
2013-11-15
Unfortunately there isn't a lot of information out there on the subject. What follows are extracts from the best articles I could find in the references shown below.
- Airbus Flight Operations Support: Proper Operation of Carbon Brakes, Guy Di Santo.
- Boeing: Operational Advantages of Carbon Brakes
Bottom line up top: minimize the number of brake applications by using longer applications. Control taxi speeds by delaying braking until about 30 knots and then bringing the speed down to about 10 knots. Keeping the brakes very cool or very warm maximizes brake life, but only the very cool range gives you maximum brake energy capability for the next maximum effort stop.
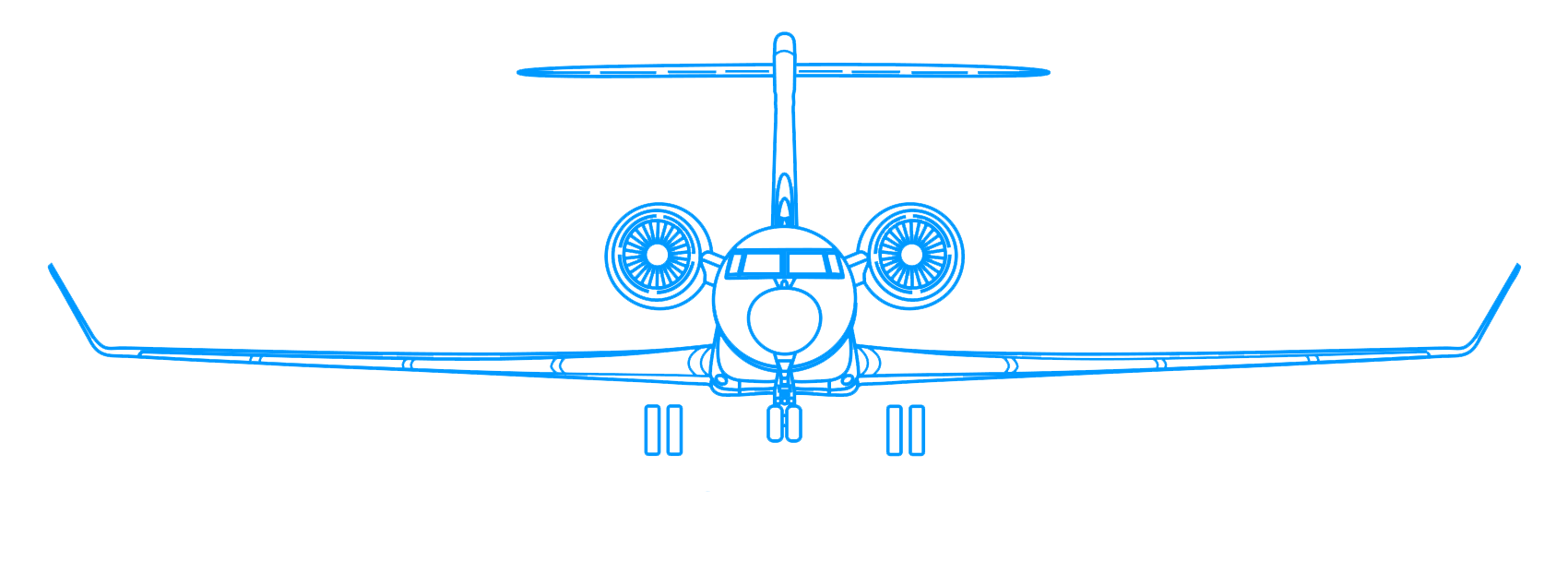
1
About Carbon-Carbon
Carbon fiber-reinforced carbon, also known as carbon-carbon, is a composite material consisting of carbon fiber reinforced with a matrix of graphite. It has a low coefficient of thermal expansion, which means it can absorb heat well without deformation. It is, however, very brittle.
Aircraft Braking Systems (ABS) Corporation puts out an excellent video: ABSC Carbon Brakes, which I have summarized thusly:
- Brake frame is made up of piston housing and torque tube. The piston housing applies the squeeze force to the heat sink.
- Heat sink is made up of alternating rotating and stationary carbon disks. The rotating disks are driven by the wheels; the stationary disks are held by keys in the torque tube.
- When hydraulics pressure is applied to the heat sink, the rotating and stationary disks are squeezed together, causing abrasive particles to form.
- At first, the abrasive particles are large and cause a lot of wear. As the heating continues, the large particles are broken down and become smaller. As they get smaller still, they become film like and wear actually decreases. Maximum wear occurs at 150°C. Once brakes are heated above this value, wear rapidly decreases.
- 79% of carbon brake wear occurs during this initial taxi out period, landing creates 19% of the wear and the taxi in only 2% of total brake wear.
- On taxi out, applying brakes at a higher speed actually decreased total brake wear. Brake wear was proportional to the number of applications.
ABSC recommended operational procedures to reduce carbon brake wear:
- Avoid riding the brakes.
- Conduct the taxi-out stop event at a higher speed.
- Minimize the number of taxi-out stop events.
2
Brake life
The number of brake applications, combined with the total duration of brake application per leg, is definitely recognized as being a major parameter governing heat pack service life. This is evidenced by the fact that airlines operating to/from congested airports, which favor multiple brake applications during taxi, generally show a 20% to 30% brake life decrease.
Source: Airbus, ¶3.1.
All brake manufacturers highlight the fact that carbon wear is heavily affected by brake temperature. The relationship between the disk temperature and the temperature indicated in the cockpit to the crew is generally not linear, and also varies from one manufacturer to the other. ABS agrees with the shape of these curves, although its data is slightly different.
Source: Airbus, ¶3.2
The typical spectrum of carbon wear versus carbon disk temperature shows an alternation of low wear and high wear areas, from low to high disk temperatures. Therefore, operational recommendations to increase carbon brake life should focus on keeping the carbon temperature outside the high wear areas. Generally speaking, to increase carbon brake life, brakes should either be operated cold or hot but not at intermediate warm temperatures.
Source: Airbus, ¶4.2
Very few aircraft manufacturers provide any literature on this subject specific to their brakes and pilots should also consider maximum brake energy limits before planning operating at the higher temperature spectrum.
Energy is theoretically not the primary parameter for carbon wear, whereas it is the most important one for steel brakes. Nevertheless, applying more energy on the brake will have a direct effect on wear due to the induced increase in brake temperature.
Source: Airbus, ¶3.2.1.
3
Preferred techniques
Taxi: Use brakes to build up brake temps to a minimum temperature of 100°C. This aids in dissipating any moisture in the brakes.
Source: G450 Cold Weather Operations Manual, Pg. 16
All recommended braking techniques should aim at reducing the number of brake applications and optimizing the carbon brake temperature. To reduce the number of brake applications, the following points should be considered:
- Do Not "Ride" the Brakes. The Airbus FCOM SOP stresses that for the taxi phase: The normal maximum taxi speed should be 30 knots in a straight line, and 10 knots for a sharp turn. As the ground speed is difficult to assess, monitor ground speed on the Navigation Display. Do not "ride" the brakes. As 30 knots are exceeded with idle thrust, apply the brakes smoothly and decelerate to 10 knots, release the brakes and allow the aircraft to accelerate again.
- Single Engine Taxi. In addition to the fuel savings it provides in congested airports, this procedure may be considered to decrease the total engine thrust when the aircraft accelerates at flight idle (e.g. at low aircraft weights), thus avoiding immoderate use of brakes during taxi. Nevertheless, the single engine taxi procedure is not advisable for short taxi times, as engine warming and engine cooling times should be respected when using this procedure.
- Alternate Left and Right Braking. This technique may be considered when slowly taxiing on normal surfaces.
Source: Airbus, ¶4.
Engine Thrust Reversers. For safety reasons, Airbus recommends the systematic selection of full reverse thrust, immediately after the main landing gear touches down, mainly because its maximum efficiency is obtained at high speed. If not selected at the beginning of the landing roll, the selection of full reverse thrust later on (if necessary) may not bring the expected help. If airport regulations restrict the use of reversers, select and maintain reverse idle until taxi speed is reached. In case of engine failure, use of the remaining reverser(s) is recommended.
Source: Airbus, ¶4.3.2.
Carbon brake wear is primarily dependent on the total number of brake applications — one firm brake application causes less wear than several light applications. Maximum carbon brake life can be achieved during taxi by using a small number of long, moderately firm brake applications instead of numerous light brake applications. This can be achieved by allowing taxi speed to increase from below target speed to above target speed, then using a single firm brake application to reduce speed below the target and repeating if required, rather than maintaining a constant taxi speed using numerous brake applications. Carbon brake wear is much less sensitive to airplane weight and speed than steel brake wear.
Source: Boeing
References
(Source material)
Airbus Flight Operations Support: Proper Operation of Carbon Brakes, Guy Di Santo.
Boeing: Operational Advantages of Carbon Brakes
Gulfstream Cold Weather Operations Manual, Applicable to All Gulfstream Large Cabin Airplanes, Includes G650, G550, GV, G450, GIV, G1159 Series, and G159 Series, Basic Issue, October 30, 2012
Please note: Gulfstream Aerospace Corporation has no affiliation or connection whatsoever with this website, and Gulfstream does not review, endorse, or approve any of the content included on the site. As a result, Gulfstream is not responsible or liable for your use of any materials or information obtained from this site.