So you are in a flight department without any Standard Operating Procedures (SOPs), you want some, but have no idea where to begin. Well let's try starting at the beginning! No, on second thought, let's start at the middle!
— James Albright
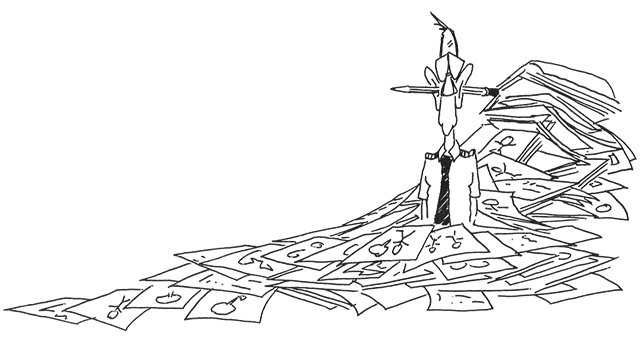
Updated:
2022-08-15
I've written a complete set of SOPs that was used by a management company I used to work for, has since been adopted by many other companies, and is currently in use at my company. These SOPs have been through countless audits, so they have been vetted. The only problem is that they are written for my operation, not yours. But you can easily adapt them.
There are eleven chapters and you might be best off by starting somewhere other than the first chapter, which is helpfully called Chapter Zero. But it would be a good idea to skim through everything: An SOP Starter Pack. Each chapter contains a presentation of the material, ideas on where to start, how to start, and a Microsoft Word Document file you can customize for you operation.
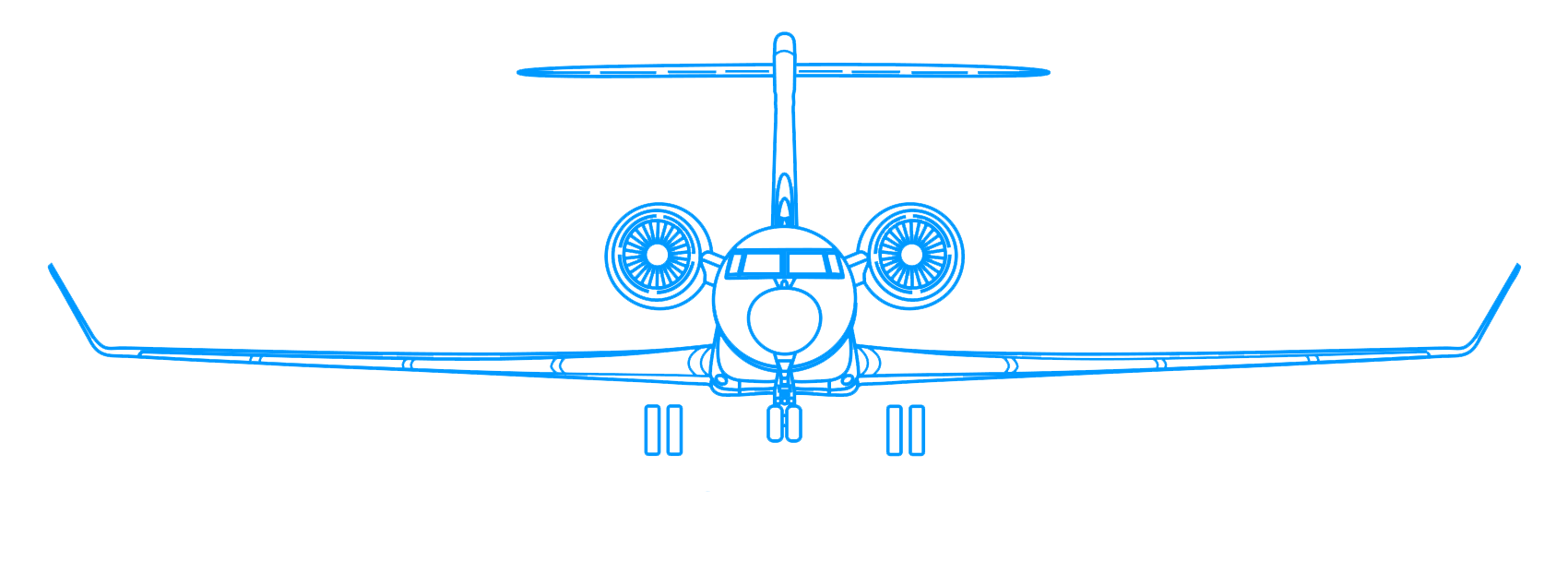
1
Why this chapter matters
This is the chapter outlines how maintenance is accomplished on your aircraft and how your mechanics go about doing their jobs.
This chapter includes:
- The maintenance department's role
- The director of maintenance's role
- Maintenance control procedures
- Inspections, unscheduled and scheduled maintenance, and functional check flights
- Records
- Minimum Equipment Lists (MELs)
- Airworthiness directives
- Weight and balance control
- Tool control
- . . . and much more
2
SMS, ICAO, ISBAO and other alphabetty spaghetti
The International Civil Aviation Administration (ICAO) dictates how things happen in aviation worldwide, with exceptions permitted within a country's airspace. In the U.S., the Federal Aviation Administration has made quite a few exceptions, but has been working over the years to whittle those down in number. Even if you never venture outside the sovereign airspace of your country, ICAO rules will impact you at some point.
If you fly internationally, you will need a Safety Management System (SMS). Even if only fly domestically, you may find that an SMS is required by your operator or your insurance broker. You will definitely find that SMS will improve how you fly.
One of the ways you can demonstrate your adherence to SMS and other best practices is to get inspected by an approved auditor, such as the International Business Aviation Council (IBAC), who can measure you against the International Standard for Business Aircraft Operations (IS-BAO).
This chapter includes references to ICAO Annexes, which are the regulations that cover international aviation. Among the references throughout this chapter:
- "NX6" — Annex 6: Operation of Aircraft
3
The chapter itself
Note: I have used "Acme Corp" as the company name. Unless that is your company's name, you should substitute your company's name wherever you see Acme Corp.
8 Aircraft Maintenance
8.1 Responsibilities of the Director of Maintenance
[14 CFR § 91.7] [NX6 2.2.3.1(c), NX6 3.8.1.1, NX6 3.4.3.1(c) and NX6 3.8.3.2]
The Director of Maintenance is responsible for the planning and control of maintenance, liaison with the FAA on maintenance topics, and liaison with persons or AMOs performing maintenance on Acme Corp aircraft. In addition, he/she shall ensure that all maintenance personnel who perform work on company aircraft have access to up to date technical and regulatory publications necessary to perform their duties. The Director of Maintenance shall remove from service any aircraft that are unsafe or that do not comply with the regulatory requirements of the FAA or the guidelines set forth in this manual. In case of absence, the duties of the Director of Maintenance will reside with the Assistant Director of Maintenance.
8.1.1 Maintenance Policies and Responsibilities
[14 CFR § 91.403] [NX6 2.6.1.1, NX6 2.6.1.2, NX6 2.6.1.4, NX6 2.6.3 and NX6 3.8.1.1]
The primary and direct responsibility of the maintenance department is to maintain company aircraft in an airworthy and dispatchable condition.
Company policy requires that the highest degree of safety standards be met. No aircraft will be returned to service unless the Director of Maintenance is satisfied that the aircraft and its equipment are airworthy.
Information resulting from maintenance and operational experience with respect to continuing airworthiness is transmitted to the FAA, as required.
Repairs, overhauls, and alterations to an aircraft must be made in a safe and efficient manner according to the standards set forth by the manufacturer’s recommendations and/or pertinent CFRs. Inspections, scheduled removal, and overhaul/replacement of life limited parts will be at intervals not exceeding those recommended by the manufacturer or approved by the FAA. Overhaul/replacement of a life limited part or assembly may be extended by written authorization from the manufacturer for a specific component. Acme Corp aircraft shall comply with mandatory S/Bs.
Acme Corp shall not allow any person in its employ and/or contract labor to perform a maintenance repair for which that person does not have the necessary experience or hold the applicable licenses unless that person is under the direct supervision of a licensed airframe and powerplant (A&P) Technician that has performed that particular task previously.
The Director of Maintenance will periodically check aircraft to verify that the aircraft registration and airworthiness certificates are current and correct.
8.2 Maintenance Control Procedures
[14 CFR § 91.403] [NX6 2.6.3, NX6 3.8.4, NX6 3.11.2.1 and NX6 3.11.2.2]
The maintenance department shall keep orderly records of all maintenance (except routine tasks) performed on aircraft, engines, appliances, etc. in accordance with appropriate CFRs.
This will enable maintenance staff to provide the following data to the Director of Aviation and to the Director of Maintenance:
a. Current aircraft status
b. Maintenance history
c. Annual budget requirements
d. Aircraft and equipment performance reliability
Records shall be maintained to accurately control the length of service life of major components of both equipment and structures.
These records shall reflect the complete service life of any component that could be interchanged from one aircraft to another, thus shortening the overall aircraft SL.
Aircraft maintenance records shall be completed each time an aircraft component or part thereof is removed or installed. These records shall reflect the history and current disposition of such components and/or parts.
A permanent record file will be maintained for each aircraft until such time that the aircraft is transferred, sold, or retired from service. This record file shall contain airframe log, engine log, 337 forms, ADs compliance form, S/ Bs compliance form, current weight and balance report, and maintenance history report compiled by a CMP.
Any deviations from the procedures in the maintenance control system require a Risk Analysis to be completed.
8.3 Elements of Aircraft Maintenance Activity
8.3.1 Preflight Inspections
Preflight inspections for Acme Corp aircraft will be performed by Acme Corp flight crew. This preflight inspection procedure shall be performed using the pilot’s operating handbook or the approved AFM. This should be complied with before every flight. When quick turn arounds are executed and aircraft have been under constant view of the Acme Corp flight crew, elements of the above procedure may be modified or eliminated if this procedure is used in an approved Preflight Inspection Checklist.
8.3.2 Postflight Inspections
Postflight inspections shall use manufacturer’s recommendations. This inspection shall be performed after the last flight of the day by an Technician experienced with the type of aircraft. If flight crews are away from home base, the Acme Corp flight crew must perform the inspection as specified in Acme Corp policies and guidelines. The aircraft should be cleaned, serviced, and flight discrepancies noted in FOS/CMP or appropriate aircraft record. Any aircraft away from home base greater than seven consecutive days shall have a postflight performed.
8.3.3 Unscheduled Maintenance
Unscheduled maintenance on Acme Corp aircraft resulting from flight activity that generates a discrepancy, including normal wear and tear, shall be performed on aircraft.
8.3.4 Scheduled Maintenance
Scheduled maintenance shall be performed on Acme Corp aircraft based on flight hours, cycles, landings, or calendar as dictated by the manufacturer or the FAA.
8.3.5 Aircraft Maintenance Inspections
Company aircraft will be maintained and inspected in accordance with factory approved programs as written by the manufacturer and approved by the FAA.
8.3.6 Maintenance Inspection Discrepancies
Discrepancies detected during postflight inspections and routine required maintenance inspections will be written up in FOS/CMP. The record will contain the description of the discrepancy, date, and person who entered it. When an item is cleared, an appropriate FAA approved technician will enter the sign off into FOS/CMP. In cases where MEL action is required additional steps will be taken to satisfy MEL requirements, and these actions will be recorded in FOS.
Discrepancies are to be addressed in a timely manner. Notify the Director of Maintenance, Director of Aviation, and crews if any major discrepancies impact the flight schedule.
Prior to the next flight the flight crew will review FOS/CMP for the current aircraft status. During the next flight the flight crew will verify that the discrepancy has been cleared.
8.3.7 Functional Check Flights
Functional check flights for Acme Corp aircraft require that an aircraft be flown before carrying passengers if it has been repaired or altered in any way that could have changed its flight characteristics or affected its operation inflight. The crew conducting the check flight must sign the appropriate aircraft record indicating that the flight was accomplished.
If a ground test/run can show conclusively the repair or alteration has not changed the flight characteristics or substantially affected the flight operation of the aircraft, then a functional check flight is not required.
8.4 Technical Records
Immediately upon finding a defect in an aircraft, or upon completing any maintenance on an aircraft, the person discovering the defect or performing the maintenance shall enter details of the event in the technical records required by applicable CFRs. If the event occurs between scheduled maintenance checks, the entries shall be made in FOS/CMP. The Director of Maintenance shall ensure that FOS/CMP entries are transcribed to the applicable airframe, engine, or component records. Details of defects found during a scheduled maintenance check, or of maintenance performed during such a check, may be entered directly in the applicable airframe, engine, or component record.
8.5 Maintenance Inspection Records
[14 CFR § 91.417] [NX6 2.6.2.1 and NX6 2.6.2.2]
Acme Corp shall ensure that these records are maintained:
a. The total time in service (hours, calendar time, cycles, as appropriate) of the aircraft and life limited components
b. The current status of compliance with applicable mandatory continuing airworthiness information
c. Appropriate details of modifications and repairs
d. The time in service (hours, calendar time, or cycles, as appropriate) since the last overhaul of the aircraft or its components subject to a mandatory overhaul life
e. The current status of the aircraft’s compliance with the maintenance program
f. The detailed maintenance records to show that requirements for the signing of a maintenance release have been met
Records shall be kept for a minimum period of 90 days after the aircraft or piece of equipment has been permanently withdrawn from service and for a minimum period of one year after the signing of the maintenance release.
8.6 MEL
[CFR § 91.213(a)(2)] [NX6 3.6.1.1]
Aircraft will have a current MEL onboard. Contents of the MEL include:
a. The appropriate FAA approved MEL
b. The assigned FAA LOA
c. MEL preamble
Equipment installed on the aircraft that is not required and is not listed on the MMEL (other than passenger convenience items such as galley equipment and entertainment devices) must be operational for dispatch. Any equipment not shown on the MEL should be considered operational, as it is part of the original aircraft type certificate.
The FAA LOA and the MEL constitutes a Supplemental Type Certificate for the aircraft and must be carried onboard the aircraft as prescribed in 14 CFR § 91.213 (a)(2).
8.6.1 MEL Repair Intervals
Users of an MEL approved under 14 CFR Parts 121, 125, 129, and 135 must complete repairs of inoperative systems or components, deferred in accordance with the MEL, at or prior to the repair times established by the letter designators. 14 CFR Part 91 MEL users do not need to comply with the repair categories, but shall comply with any provisions defining a repair interval (flights, flight legs, cycles, hours, etc.)
8.6.2 Deferred Rectification of Defects
[NX6 3.4.5.3]
Discrepancies shall be rectified before further flight of the aircraft, except as provided in this section. Where permitted by applicable FAA regulatory provisions, aircraft having outstanding discrepancies may be operated subject to these procedures:
a. Where an MEL has been approved and the list includes limits on the amount of time equipment may be inoperative, those limits apply
b. Where the MEL does not specify time limits, the aircraft may be operated following discovery of a discrepancy. This provision is conditional to the following procedure:
i. The pilot reports and coordinates the discrepancy deferral with the Director of Maintenance, who coordinates the authorization of the deferral
ii. If required, he/she will seek advice from a qualified AMO that the discrepancy does not invalidate the aircraft Certificate of Airworthiness
iii. The authorization shall be recorded in the FOS/CMP and original filed in the aircraft record
iv. The FOS/CMP entry shall specify the reason for the deferral and the latest date by which the discrepancy must be corrected, but no longer than at the next scheduled maintenance event
v. Rectification shall take place as soon as practical following discovery of the discrepancy
8.6.3 MEL Flight Discrepancies
The procedures for handling flight discrepancies will be as follows:
a. The flight crew will list the discrepancy on FOS/CMP
b. The flight crew will notify maintenance of the discrepancy
i. If en route to an airport other than home base, notification will be upon arrival at that destination. The flight crew will place an inoperative placard above the affected unit
ii. If en route to home base, aircrew will notify maintenance by flight phone or as soon as possible
c. Upon arrival at home base, flight crew and maintenance will debrief
d. Maintenance will take corrective action to clear the discrepancy and return the aircraft to service
If the discrepancy cannot be cleared due to parts availability or scheduling, the aircraft will not be dispatched until approved by the Director of Maintenance.
8.7 Technical Dispatch
Technical dispatch of aircraft shall be by means of FOS/CMP. Immediately following completion of any item of scheduled maintenance specified by a maintenance schedule, AD, or other mandatory requirement, the Director of Maintenance shall review the aircraft technical records to determine the date, air time, or operating cycles when the next scheduled maintenance activity will become due and make an entry to that effect in the log.
Before each flight, the PIC shall examine scheduled maintenance requirement and the current list of outstanding defects in the aircraft FOS/ CMP to decide whether the flight may take place. If in doubt as to the time remaining to complete maintenance tasks or the acceptability of defects, the PIC must contact the Director of Maintenance.
8.8 Airworthiness Directives
[NX6 2.6.3]
The Director of Maintenance shall maintain a system to ensure that aircraft are in compliance with applicable ADs and other mandatory maintenance requirements. He/she shall examine aircraft records upon appointment to the position and upon each acquisition of a new aircraft to verify this compliance. The Director of Maintenance shall review new and revised ADs upon receipt to determine if they are applicable. He/she shall enter details of applicable ADs and details of directives pertaining to the aircraft make and model in the appropriate airframe, engine, propeller, or component technical record. The Director of Maintenance shall determine the date, air time, or operating cycles when the actions specified in the directive must be taken. If the required actions are due before the next scheduled maintenance activity, he/she shall make the necessary entries in FOS/CMP in accordance with this chapter.
8.9 Maintenance Arrangements
[NX6 3.8.3.2]
Aircraft maintenance shall be performed by the company’s own authorized qualified Technician or AMO. An AMO shall hold proper license, ratings, and scope for the work to be undertaken and authorized in writing in the form of a contract, purchase order, or letter. Each request for maintenance shall specify that the work be performed and certified in accordance with the applicable requirements of the CFRs and in accordance with this document. The Director of Maintenance shall make planned maintenance arrangements.
The Director of Maintenance shall be notified of unplanned maintenance activities as soon as practical. In the case of unplanned maintenance away from home base, the PIC may request a written record of the maintenance.
The selection of any qualified Technician or AMO to perform the maintenance may be coordinated with the PIC, however, he/she should confirm that they hold a certificate/license appropriate to the work to be done and that the specific scope and limitations of the work to be done are covered under the work order. Relevant sections of the appropriate manuals will be supplied to each person who performs or certifies work. If in doubt, they should consult with of the Director of Maintenance.
Projected work is described and specified in the fullest detail possible. Estimates of cost are to be as accurate as possible. Once an estimate for work has been established, a purchase order or agreement between Acme Corp and the AMO shall be drafted. The AMO shall provide a delivery schedule. If the agreed completion date cannot be met, the AMO must immediately notify Acme Corp as soon as possible. Upon completion of the work an entry must be made in the appropriate aircraft records by the AMO reflecting the work that has been done in accordance with applicable requirements of the CFRs.
8.9.1 Outside Vendor Approval
Out Source Vendors will be vetted before they perform any tasks on company aircraft that they are trained, and follow the appropriate policies and procedures approved the aircraft manufacture program and company requirements.
8.10 Aircraft Defects
Immediately upon finding a defect in an aircraft, or upon completing any maintenance on an aircraft, the person discovering the defect or performing the maintenance shall enter details of the event in the applicable technical records required by applicable aviation regulations.
8.11 Recurring Defect Control
At intervals not to exceed three months, the Director of Maintenance shall review the aircraft technical records to detect any recurring defects. Any defect that has occurred three or more times within the past three months or the past 20 flight segments shall be reported by the Director of Maintenance to the maintenance staff or AMO responsible for maintenance. If a defect that has been reported as a recurring defect occurs again within one month of receiving the report, the Director of Maintenance shall ensure that the corrective action includes a complete investigation of the affected system(s), taking into consideration previous occurrences of the defect and the actions taken to correct them. FOS/CMP entry for rectification of the defect shall indicate that a recurring defect investigation has been carried out.
8.12 Aircraft Weight and Balance Control
The Director of Maintenance shall maintain and retain weight and balance reports and amendments for aircraft. Details of the empty weight and center of gravity of each aircraft shall be kept in the aircraft log and onboard the aircraft. Aircraft will be weighed and/or recalculated, and the new center of gravity calculated and recorded. This information will be provided to the Director of Aviation to be used in the computations necessary for flight planning.
8.13 Preventative Maintenance and Servicing
No Acme Corp employee shall perform any preventative maintenance, aircraft servicing, ground handling, or inspection without first being trained and authorized to do so. All preventative maintenance defined under 14 CFR part 43 and aircraft servicing shall be accomplished in accordance with the methods and the recommendations of the aircraft manufacturer and applicable regulations under 14 CFR part 43. The individual performing the work is responsible for recording the maintenance completed.
No flight crewmember (Pilot) is authorized to perform aircraft maintenance. Any preventative maintenance or servicing performed will only be allowed after the crewmember has received training in that operation.
8.14 FOD
The Director of Maintenance should ensure that general visual inspections of the maintenance hangar floor, work areas, shop areas and ramp are made on a daily basis. The scrubber machine will be used to clean the hangar floor on a regular basis or after maintenance has been completed on an aircraft. All department personnel should watch for loose items and debris on the floors and ramp that could lead to FOD incident.
NOTE: FOD prevention is everyone’s job.
8.15 Parts and Material Control
Parts required for elementary work and servicing shall be managed by the Director of Maintenance. Fuels, oils, lubricants, and cleaning materials shall be kept in closed containers, clearly marked with the contents, and handled in accordance with applicable industry recommendations. No fluids shall be dispensed from any unmarked container. 8130s will be kept until the part is installed, then retained with the aircraft logs.
8.15.1 Spare Parts Inventory
Acme Corp spare parts and equipment should be purchased only from manufacturers, authorized dealers or distributors, or certified repair stations. These items should be tagged to show manufacturer part number, TSN, TSO, SN, expiration date, whether new or repaired, whether removed from service in serviceable condition or not, and the reason for removal,. Any condemned/expired parts should be destroyed so they cannot be used on an aircraft again. Parts being held for instructional purposes should be tagged so they cannot be returned to service.
8.15.2 Minimum Standards for Equipment
Acme Corp shall follow the minimum performance and quality control standards for materials, parts, or appliances used on Acme Corp aircraft through technical standard orders that have been established by the FAA. This will ensure that the equipment will perform its intended purpose under specified conditions.
Approved flotation gear, safety belts, and anti-collision lights are some items that will require approval. Any equipment not approved by technical standard order should be given careful consideration to equipment manufactured under voluntary minimum standards.
To ensure that quality and legitimate parts are used in all repairs, replacement products and parts must be purchased from sources that can certify the product or part was produced under a technical standard order or parts manufacturer approval issued by the FAA. Pilots, Technicians, operators, manufacturers, and accident investigators should report major aircraft technical malfunctions and defects of parts, materials, or appliances to the local FAA office or on FAA form 8010-4.
8.16 Maintenance Tooling
8.16.1 Technician Tools
Technicians will utilize company provided tools, for tool control purposes, to perform maintenance on company aircraft. Standard and metric tooling may be necessary depending on the aircraft, engines, etc. Company will provide secure storage for aircraft tools.
8.16.2 Shop Tools
Acme Corp will provide all necessary shop tools to maintain aircraft. Examples of such tools are measuring devices, torque wrenches, tugs, hydraulic units, etc.
8.16.3 Tool Calibration
Shop and technician tools used to make airworthiness determinations will be calibrated annually to manufacturer specifications. The Director of Maintenance will maintain calibration records. Any tools that are maintained out of calibration will be marked as being for reference only.
8.16.4 Tool Control
The Director of Maintenance will use the Gulfstream CMP tool control program, listing all tools and include calibration expiration dates. A SNAP- ON Level 5 ATC Tool Control System will be the source of tools used on the aircraft to ensure tools and equipment are all accounted for at the completion of the work. After maintenance is performed on the aircraft, maintenance personnel will confirm the box indicator show the drawers in white (drawers in yellow indicate tools removed) indicating all tools have been returned.
8.17 Flight Authorization/Maintenance Release
[14 CFR § 91.405 and 91.407]
[NX6 2.6.1.3, NX6 2.6.4.1, NX6 2.6.4.2, NX6 3.8.5.1 and NX6 3.8.5.2]
An aircraft will not be operated until the Director of Maintenance or the Assistant Director of Maintenance has released the aircraft in writing. A maintenance release shall be completed and signed, as prescribed by the FAA, to certify that the maintenance work performed has been completed satisfactorily and in accordance with data and procedures acceptable to the FAA.
Maintenance release shall contain a certification that includes:
a. Basic details of the maintenance performed
b. The date such maintenance was completed
c. When applicable, the identity of the approved maintenance organization
d. The identity of the authorized person or persons signing the release
The detailed maintenance records to show compliance with all requirements for the signing of a maintenance release are kept for a minimum period of one year after the signing of the maintenance release, or until the work to which it relates is repeated or superseded, whichever is longer.
8.18 Special Flight Authorization
The Director of Maintenance shall be responsible for applications made to the FAA for aircraft special flight authorities and is authorized to make any required declarations for this purpose on behalf of the company.
Essential crew only (no passengers) shall be carried on special flights. The flight shall be conducted in accordance with all conditions specified by the FAA.
8.18.1 Special Flight Request Procedures
Contact local FAA office where aircraft is located and talk with a maintenance inspector.
The special permit request should include:
a. Make, model, SN, and registration number of the aircraft
b. Departure location
c. Arrival location
d. Reason for special permit request (maintenance, etc.)
e. Date aircraft will depart. The FAA will usually grant a ten day window for the special flight
f. Request IFR flight if practical and needed. Normally the FAA grants a special permit for daylight VFR only
g. Ask for permission for Technician to accompany aircraft if practical. Normally special permits are issued to include only personnel needed to conduct the flight
h. Applicable AD notes must be complied with prior to special flight (unless it must be ferried to comply with an AD note)
i. Aircraft must be inspected by a Technician or repair station prior to the special flight, and a statement must be placed in the Flight Logbook, for example: “This aircraft has been inspected and is safe for special flight from to .” Signed
j. Copy of the special permit must be placed as instructed per the text of the special permit
8.19 Recency of Experience
In order to be eligible to sign a maintenance release, a Technician must have at least six months experience within the previous 24 months in the inspection, servicing, or maintenance of aircraft systems in accordance with the privileges granted by the license held in relation to that maintenance release.
4
Where to start
This is a chapter that really needs to come from your maintainers with consultation with your local FAA Primary Maintenance Inspector. If all of your maintenance is contracted out, then you should consult with someone at your manufacturer for some advice.
Our example manual might cover more topics than you need, or maybe not enough. But it will get you started.
5
How to start
With each chapter it is a good idea to:
- Talk it over with your team, get their ideas on how to best accomplish the chapter's goals given your unique situation. All ideas are worth considering, write them down in a way the person offering it agrees fully captures the idea.
- Give the team time to digest the proposals.
- Ask the people with the right background to massage the ideas into concise concepts, then have your best wordsmith turn those concepts into paragraphs. The paragraphs need to be in plain spoken sentences, easy to read, and written at the fifth grade level of comprehension.
- Present the ideas to the group. Listen to any objections and seek consensus. Repeat the entire process if needed, but understand that the person in charge will eventually make a decision that becomes department policy. At the very least, stress that each policy can be tested on a trial basis and looked at again in the future.
6
Word file
You can download a Microsoft Word "docx" file of this chapter here: Acme Corp Operations Manual Chapter 8 - Aircraft Maintenance.
Remember, this is your blank canvas to customize as you see fit.