The Safety Assessment of Foreign Aircraft (SAFA) program has been with us since 1996 and we have been expecting ramp inspections throughout Europe ever since. The European Union made it mandatory for its member states to do these SAFA checks and they seem to trip us up now and then. You may think that as long as you are doing things the best way possible there won't be any issues. The problem is "the best way possible" is in the eye of the beholder. You may think, for example, that having an MMEL is good enough for Uncle Sam so it ought to be good enough for everyone else. Not so.
— James Albright
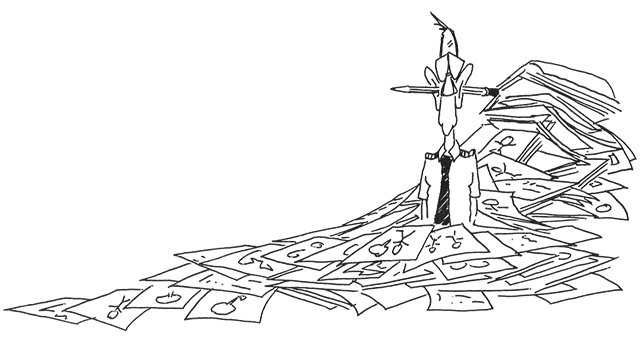
Updated:
2023-05-04
You may have also heard that SAFA has been replaced by the "RIP". That is also not true. The Ramp Inspection Program (RIP) encompasses SAFA and SACA, where the second acronym is intended for Community Aircraft, those from EU member states. Inspectors use specific guidance to check 53 areas. The traditional way to prepare for an inspection is with an abbreviated checklist.
2 — An overview, for U.S. operators
4 — Deviation categories and Pre-Described Findings (PDFs)
The remaining topics deserve their own articles, selecting the link will take you there:
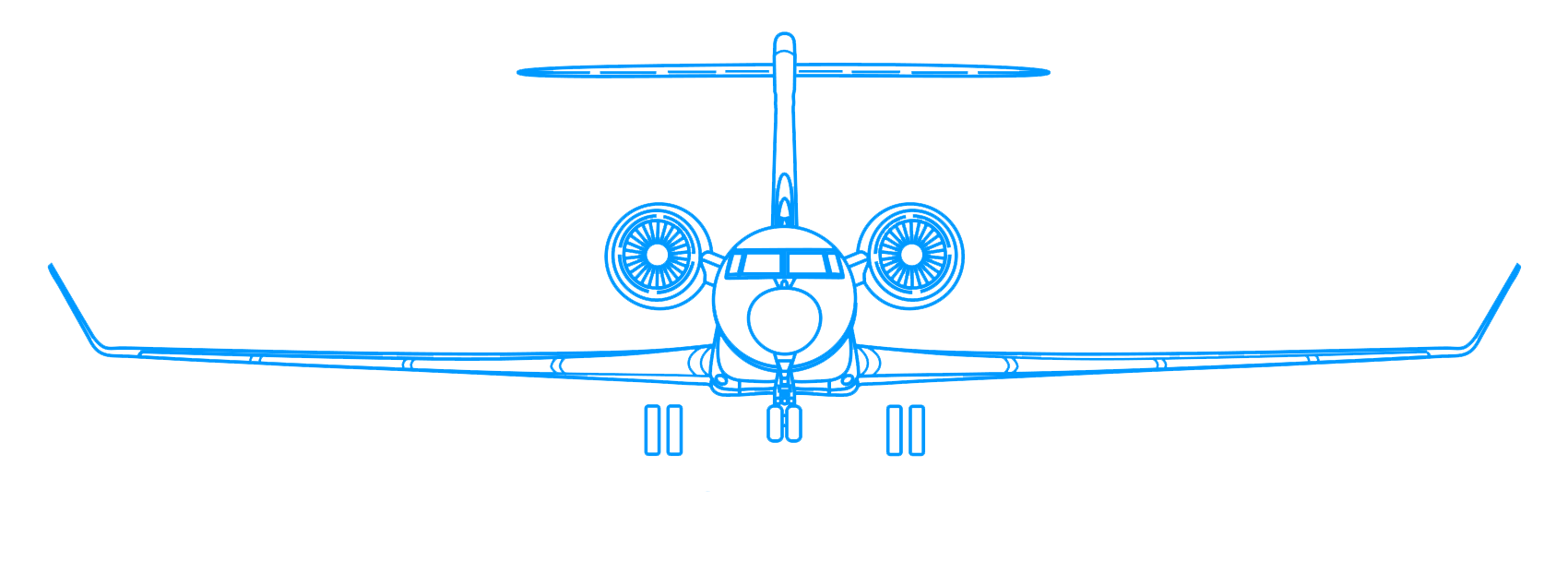
1
Abbreviated checklist
These are the inspection items used by the SAFA ramp inspector. You will find this checklist reprinted at many aviation websites. In my opinion, it is little more than a grade sheet and useless for preparing a flight operation for a ramp inspection. To be better prepared, I recommend the Expanded Checklist.
Code | Item | |
A. Flight Deck | A01 | General condition |
A02 | Emergency exit | |
A03 | Equipment | |
Documentation | A04 | Manuals |
A05 | Checklists | |
A06 | Navigation/instrument charts | |
A07 | Minimum equipment list | |
A08 | Certificate of registration | |
A09 | Noise certificate (where applicable) | |
A10 | AOC or equivalent | |
A11 | Radio license | |
A12 | Certificate of Airworthiness | |
Flight Data | A13 | Flight preparation |
A14 | Mass and balance calculation | |
Safety Equipment | A15 | Hand fire extinguishers |
A16 | Life jackets / flotation device | |
A17 | Harness | |
A18 | Oxygen equipment | |
A19 | Independent portable light | |
Flight Crew | A20 | Flight crew license/composition |
Journey Log Book / Technical Log or Equivalent | A21 | Journey log book or equivalent |
A22 | Maintenance release | |
A23 | Defect notification and rectification (Int. Tech Log) | |
A24 | Preflight inspection | |
B. Safety / Cabin | B01 | General internal condition |
B02 | Cabin crew station and crew rest area | |
B03 | First aid kit / emergency medical kit | |
B04 | Hand fire extinguishers | |
B05 | Life jackets / flotation device | |
B06 | Seat belts and seat condition | |
B07 | Emergency exit, lighting and independent portable light | |
B08 | Slides / life-rafts (as required), ELT | |
B09 | Oxygen supply (cabin crew and passengers) | |
B10 | Safety instructions | |
B11 | Cabin crew members | |
B12 | Access to emergency exits | |
B13 | Stowage of passenger baggage | |
B14 | Seat capacity | |
Aircraft Condition | C01 | General external condition |
C02 | Doors and hatches | |
C03 | Flight controls | |
C04 | Wheels, tyres and brakes | |
C05 | Undercarriage, skids/floats | |
C06 | Wheel well | |
C07 | Powerplant and pylon | |
C08 | Fan blades / propellers, rotors (main/tail) | |
C09 | Obvious repair | |
C10 | Obvious un-repaired damage | |
C11 | Leakage | |
Cargo | D01 | General condition of cargo compartment |
D02 | Dangerous goods | |
D03 | Cargo stowage | |
General | E01 | General |
2
An overview, for U.S. operators
Historical
The SAFA RIP began in the EU community in 1996 and has evolved into a ramp inspection tool that is utilized by at least 49 countries. The EU RIP is managed by the European Aviation Safety Agency (EASA) and continues to focus on EU and non-EU aircraft landing at airports within EU member states and other non-EU participating states. The FAA signed a cooperative arrangement with EASA to receive safety information and notices from the SAFA RIP in 2011. Aircraft suspected of noncompliance with safety standards established by the International Civil Aviation Organization (ICAO) have a greater chance of a ramp inspections.
Source: InFO 20003
Procedural
The ramp inspections carried out by EU RIP participating member states follows a common procedure, using a checklist covering the array of inspection areas based on ICAO standards. It is EASA policy that ramp inspections will not delay aircraft except for safety reasons. Ramp Inspection Programme inspectors may not be able to complete all checklist items if an aircraft has a short turnaround time. Regardless of if an EU RIP inspection is completed in its entirety or not, it is an on-the-spot ramp inspection that does not substitute regulatory oversight of the state of the operator or the state of registry, as applicable. A completed RIP inspection does not guarantee the aircraft is airworthy; instead, it focuses on evaluating compliance with 53 inspection areas that consist of ICAO requirements and specific EASA criteria.
Source: InFO 20003
The checklist used by EU RIP inspectors is available for download to help you prepare: EU SAFA Inspection Instructions on the Categorisation of Ramp Inspection Findings. Additionally, I have broken down the checklist into sections with the pertinent guidance: Expanded Checklist.
Findings
- When an EU RIP ramp inspection results in a finding identified within a checklist item, it is categorized as a 1, 2, or 3. The category is dependent upon the magnitude of the deviation from the international requirements and the impact on safety associated with the noncompliance.
- Category 1 Finding. A Category 1 finding is considered a minor deviation and is reported to the pilot-in-command (PIC) (operator).
- Category 2 Finding. A Category 2 finding is considered a significant deviation from safety standards. The findings are reported to the operator and the oversight authority of the operator. For U.S. operators, Category 2 findings are reported to the Federal Aviation Administration (FAA).
- Category 3 Finding. A Category 3 finding is one that has a major impact on safety. The reporting requirements are the same as Category 2. Category 3 findings are expected to be corrected by the operator before the aircraft departs either by correcting the deficiency or by imposing limitations or restrictions on the operation of the aircraft. These limitations may be imposed by the inspecting authority.
- Any U.S. operator who receives a EU RIP ramp inspection and is issued a Category 1, 2, or 3 finding is responsible for all immediate and future actions required to clear the finding to the satisfaction of the EU RIP pursuant to and in accordance with the requirements of Title 14 of the Code of Federal Regulations part 91, § 91.703. Failure by the operator to respond within 60 days of notification of inspection findings, failure to address repetitive findings, or failure to address safety items could result in operational restriction(s) applied to that operator, up to and including rescinding flight authorizations and barring the operator from future operations into applicable state(s).
Source: InFO 20003
A ramp inspection is possible anywhere in the world, an EU RIP is possible at: Albania, Armenia, Australia, Austria, Azerbaijan, Belgium, Bosnia and Herzegovina, Bulgaria, Croatia, Cyprus, Czech Republic, Denmark, Estonia, Finland, France, Georgia, Germany, Greece, Hungary, Iceland, Ireland, Israel, Italy, Latvia, Lithuania, Luxembourg, Malta, Republic of Moldova, Monaco, Montenegro, Netherlands, Norway, Poland, Portugal, Romania, Serbia, Slovak Republic, Slovenia, Spain, Sweden, Switzerland, The Republic of North Macedonia, Turkey, Ukraine, and United Kingdom. Also participating: Canada, Morocco, Singapore, United Arab Emirates.
What you need to know: You are required to cooperate. Most findings will not have an operational impact but will have to be answered. If they aren't you may find yourself a target of future inspections that will be much more thorough. An inspector can ground you if a Category 3 finding cannot be corrected prior to your departure.
3
How it normally goes down
The good folks at ops.group have a huge membership and the intel is great. Here is what they have found:
Process
The flight selected will either be your last of 6 legs for the day, or after a grueling 12 hour jetlag-inducer, or at 3am when you were thinking about a quick nap during the turnaround. This much is guaranteed.
As you pull on to the stand, you will notice more yellow vests than normal hanging around.
Two of these will be your friendly ramp inspection team (to be fair, they almost always are). A short time later, those yellow vests will be in the cockpit, and the first request will be for a look at your license, medical, aircraft documents (like Insurance, Airworthiness), and flight paperwork. Make sure you’ve done your fuel checks and there are a few marks on the flight plan.
If you get a good cop, bad cop scenario, one will disappear down the back (this will be the nice guy) and check the cabin, while the first will stay and ask you tough questions about the TCAS system.
Some time later, you’ll get a list of findings. The average check is probably about 30 minutes.
You can be guaranteed they will always have at least one finding – which will probably be obscure.
Sign off the checklist, and you’re on your way.
A few points
The Inspectors can ask you for manuals, documents, or guidance – but they are not supposed to test your knowledge of procedures, regulations, or technical matters. This doesn’t always happen in practice – so if you get a tough question – just say “I don’t know” – and let them note it if they want to. This isn’t a classroom test.
This guidance is given to Inspectors: Delaying an operator for a non-safety related issue is not only frustrating to the operator, it also could result in unwanted human factor issues with possible negative effects on the flight preparation. They can (should) only delay your flight for a safety related issue.
Remember, it’s not you that’s being inspected. It’s your aircraft. If you’re uncomfortable with the questions, get them noted and allow your operator to discuss later.
Every inspector is a little different. Work with them and you’ll find that 90% of your ramp checks will be over in 20 minutes with little issue.
Private Operators – especially in GA (even more so under the 5700kg mark) – are far less likely to get ramp checked. EASA guidelines do apply to General Aviation, but they are far more interested in Commercial Operators.
The items checked during ramp checks are based on a risk based approach and can differ from operator to operator (for example depending on findings raised during previous inspections). Meaning that operators who get ramp checked with findings will most likely get ramp checked again, to see if they’ve sorted out the problems!
EASA regulations requiring alcohol testing during ramp checks will take effect across all SAFA countries in Aug 2020. But some countries have already started doing this: Austria, Belgium, Czech Republic, France, Germany, Greece, Iceland, Ireland, Italy, Netherlands, Portugal, Spain, Switzerland, UK, and Singapore.
Common Findings
Fuel Calculation and Flight Routing: Alternates must be planned with a SID/STAR routing. In many parts of the world it is common to plan DCT, but not in many European countries. Non-compliance during a ramp inspection could lead to either a Cat 2 finding when sufficient fuel was taken into account such that the required fuel is above the minimum, or a Cat 3 finding when this was not the case.
You cannot point to your flight plan and say you have more than enough fuel to fly the expected alternate routing, it has to be on the flight plan or in a second flight plan you can point to. More about how to do this: SAFA-Alternate Fuel.
PRNAV/RNAV-1 capability – non-compliance constitutes a Cat 3 finding when landing at airports (such as EHAM/Amsterdam) that require it. The finding will also be reported to the aeronautical oversight department who can give fines for such violations.
There are airports where the usual approach requires PRNAV/RNAV-1 and some where the only approach in use requires it. If you don't have the necessary authorizations (LOA or Ops Spec) you can bet the inspectors will be waiting for you.
Filing incorrect flight plans – specifically saying you are 8.33 MHz equipped and PRNAV/RNAV-1 capable. Again, this could lead to findings and fines beyond the RIP programme. An easy one to miss.
Keep in mind that flight plan codes have changed over the years and the codes you have been using might be wrong today. (This got me in an LOA application.) More about this: Flight Plans.
TCAS 7.1 – the TCAS 7.1 requirement became mandatory in EU Airspace from 1st of December 2015 and became a worldwide standard under ICAO from 1st of January 2017. One to also watch out for if operating to EU overseas territories in the Caribbean where this requirement has also been implemented and during ramp inspections is enforced the same way. More about this: SAFA and TCAS 7.1.
What you need to know: Inspectors are more likely to show up after you arrive than when you depart. They don't want to impact your departure schedule. While inspections of Part 91 aircraft have been rare, they do occur. Various country inspection agencies promise they will be increasing these inspections.
4
Deviation categories and Pre-Described Findings (PDFs)
- For each inspection item, 3 categories of possible deviations from the standards have been defined. The findings are categorised according to the potential influence on flight safety. This means that a CAT 1 finding is considered to have a minor influence on safety. A CAT 2 finding may have a significant influence and a CAT 3 finding may have a major influence on safety.
- Note: Any other safety relevant issues identified during a ramp inspection (SAFA /SACA), although not constituting a finding, can be reported as a General Remark (CAT G) under each inspection item, for example: missing life vests for flights conducted entirely overland.
- The finding should be categorised according to the list of Pre-Described Findings (PDF) listed below. In the PDF list the description, categorisation and reference to the applicable standard is given. Although the list of PDFs is as complete as possible, it cannot cover all possible deviations that may occur.
- The PDF list is intended to be used by the inspector to guarantee a common description and categorisation of findings. The inspector should make use of this list in the majority of situations and should always privilege the use of PDF while reporting findings in the EASA database. In those cases where there is no appropriate PDF, the inspector should, based upon his proficiency and the impact on aviation safety, make a sound judgment into which category the finding needs to be placed. The ramp inspection tool allows for findings to be entered by the user. While inserting a User Described Finding (UDF) in the EASA database, the inspector should make sure to always report the associated Standard Reference representing the basis for the identification of the finding.
Source: EU SAFA Inspection Instructions on the Categorisation of Ramp Inspection Findings, Introduction
What you need to know: It all ends with a list of Pre-Described Findings (PDFs) which are an easy way for "them" to place all of their findings into 53 different categories. Those categories correspond to items in the inspection checklist.
5
Centralized database
- The backbone of the EU Ramp Inspection Programme is the centralised database, which is managed and maintained by EASA, in Cologne, Germany. The inclusion of reports in the database remains a responsibility of the individual Aviation Authorities of the Participating States.
- Data contained in the database is confidential and therefore shared only with other Participating States and not available to the general public. The database can be accessed by all Aviation Authorities of the Participating States via the (secured) Internet. At present, all Aviation Authorities are connected on-line to the database. In addition, read-only access is provided to the European Commission and ICAO.
- EASA is performing regular analysis of the centralised database. The regular analysis is conducted every 3-4 months, with the aim at identifying safety concerns and worrying trends which should be addressed before they become a threat to the safety of international aviation. Since September 2011, Operators and their Aviation Authorities (NAAs) can register online to that database; obviously, the access is limited to ramp inspection reports on their own aircraft. Since the user management is delegated to the local Aviation Authorities, these authorities need to have obtained access to the database before the operators can register themselves. Once the operator and/or the NAA has access, any follow-up information on the inspection can be uploaded to the database; this lowers the burden of the administrative workload considerably. Details on the registration process can be found in the FAQ document available at the login page of the SAFA database.
What you need to know: Findings from one inspector are viewable by all inspectors and can actually make it more likely that you will be inspected again, even in different countries, looking for the same finding.
From readers and the International Business Aviation Council (IBAC):
- A13 — Flight preparation
- A14 — Weight and balance calculations
- A07 — MEL
- A05 — Checklists
- A06 — Navigation, instrument charts
Selection of a destination alternate that cannot be used as an alternate in the French AIP or for which a required PPR hasn't been obtained, no weather charts, and unrealistic alternate flight planning. There were over 100 such findings in 2021.
The actual headcount or baggage numbers were wrong.
These were mostly mismatches of equipment on the aircraft and that listed in the MEL.
Different versions of the checklist were found, outdated checklists, and missing checklists.
Outdated navigation databases or charts, use of an unapproved EFB, and no storage device for the EFB.
Other Updates
- The SAFA requirements apply to both commercial and general aviation aircraft, and of roughly 10,000 inspections a year conducted in EU member states, only around 5 to 7 percent are in the latter category.
- In most cases, batteries and the electronic devices that contain them should be carried into the cabin with the passenger’s hand luggage. NBAA is urging operators to review their dangerous goods storage program to ensure they are correctly handling these materials.
- Since the EU introduced its alcohol testing program in February 2021, SAFA inspectors have tested 9,000 crew members, generally as part of a wider inspection but in around 10 percent of cases as a standalone process.
Source: Operators Need to Be Up to Speed on European Inspection Rules
References
(Source material)
EU SAFA Inspection Instructions on the Categorisation of Ramp Inspection Findings, INST.RI.01/003, 20/03/2019
Gulfstream GVII-G500 Aircraft Maintenance Manual, Revision 4, June 28/19
Gulfstream GVII-G500 Airplane Flight Manual, Revision 4, August 29, 2019
InFO 20003, Information for Operators, U.S. Operator Responsibilities Associated with the European Union Ramp Inspection Program (RIP), formerly referred to as EU's Safety Assessment of Foreign Aircraft (SAFA) RIP.
Operators Need To Be Up to Speed on European Inspection Rules, AINonline, May 3, 2023
Ops Group, Avoiding the Pain of a Ramp Check
Please note: Gulfstream Aerospace Corporation has no affiliation or connection whatsoever with this website, and Gulfstream does not review, endorse, or approve any of the content included on the site. As a result, Gulfstream is not responsible or liable for your use of any materials or information obtained from this site.